Lucas Epp, engineering manager of StructureCraft Builders Inc. says if Canadian construction will prosper in the 21st century, it needs to learn from such industries as automotive assembly and aerospace and make more use of advanced technology.
Construction is still very much an old-school industry, he says.
“Compared to automotive and aerospace, which are dominated by a few big manufacturers, construction is fragmented and decentralized, with many players of different sizes,” said Epp. “And, unlike automotive and aerospace, there is great variability in the sizes, shapes and details of the buildings they make.”
Borrowing from modern automation and assembly line techniques, StructureCraft (located in Abbotsford, B.C.) engineer and build mass timber and free-form timber structures.
The company calls itself “an industry leader in the mass timber revolution, answering the pressing need for increased quality and construction efficiency, at the same time reducing site erection time and risk.”
From its 18-month-old, 50,000-square-foot factory in the Fraser Valley, StructureCraft manufactures and sources a range of such mass timber products as dowel-laminated timber (DLT), cross-laminated timber (CLT), nail-laminated timber (NLT) and glulam, as well as steel components.
To make these wood products, Epp says StructureCraft employs presses, finger-jointing lines, CNC (computer numerical control) machines and other automated manufacturing machines, plus the human machine operators to run them.
“Pre-fabrication has a number of benefits for us,” said Epp. “It’s faster, less expensive and the quality is better.”
In addition to its main manufacturing facility in Abbotsford, StructureCraft employs temporary prefabrication facilities when the need arises.
One example is the company’s part in the project to construct the T3 Building (timber, technology, transportation) in Minneapolis, one of the largest modern mass-timber buildings in the U.S.
StructureCraft arranged with a supplier to ship glulam members to a temporary pre-fabrication plant near Minneapolis, where it pre-installed connection steel and reinforcing screws to the glulam.
The company decided to use NLT for the mass-timber floor and roof panels which span the glulam post and beam framework because of its cost-effectiveness and rapid procurement times.
To assemble the panels, StructureCraft designed a temporary pre-fabrication facility in an old warehouse near the Winnipeg airport, where it also determined panel sequencing and receiving between the Manitoba capital and Minneapolis.
The Winnipeg StructureCraft crew put together over 1,100 NLT panels with unique screw reinforcement and notches to within 1/8-inch tolerance.
Then everything was trucked 400 miles south to the building site in downtown Minneapolis, where StructureCraft crews installed the 180,000 square-foot timber superstructure in only 9.5 weeks.
StructureCraft also used a temporary manufacturing site in its work on the expansion of the National Arts Centre (NAC) in Ottawa.
StructureCraft was engaged to provide design-assist, structural engineering, fabrication and supply services to the addition to the NAC in time for Canada’s 150th birthday in 2017.
The façade has columns 30 feet-50 feet long that support 30 roof panels of different sizes and shapes.
The panels are made of trapezoidal glulam segments of varying depths that are fastened together by 65-foot-long steel plates running along one side of each panel.
An acoustic panel is supported at middle height inside each panel, hiding from view a complex web of electrical conduits, sprinkler pipes and theatrical equipment that were all installed off-site.
“To reduce transportation costs and to deal with the massive covered space that was required to pre-fabricate these panels, we set up assembly lines in a rented facility outside Ottawa and brought in the equipment we needed,” said Epp. “Work there could be challenging, because sometimes there were as many as three or four trades inside the facility to assemble the individual panels.”
Epp says temporary pre-fabrication facilities often come in handy for StructureCraft, but they are not about to replace the company’s permanent factory in Abbotsford.
“Whether we decide to use a temporary facility or not depends on a number of different variables,” said Epp. “We need to consider such factors as transportation distance from the pre-fabrication facility to the construction site, how much additional space and in what configuration it is needed and, if we require additional equipment, whether to buy, rent or lease it.”
Temporary facilities can also have a down-side, Epp says, if start-up costs are high.
“We’ll use temporary facilities in the future, depending on the project at hand, and after we’ve calculated all of the costs and benefits involved,” said Epp.
In fact, in 2019 StructureCraft is using a storage facility on the campus of the University of Idaho, where it is building a new basketball arena, as a temporary pre-fabrication site.
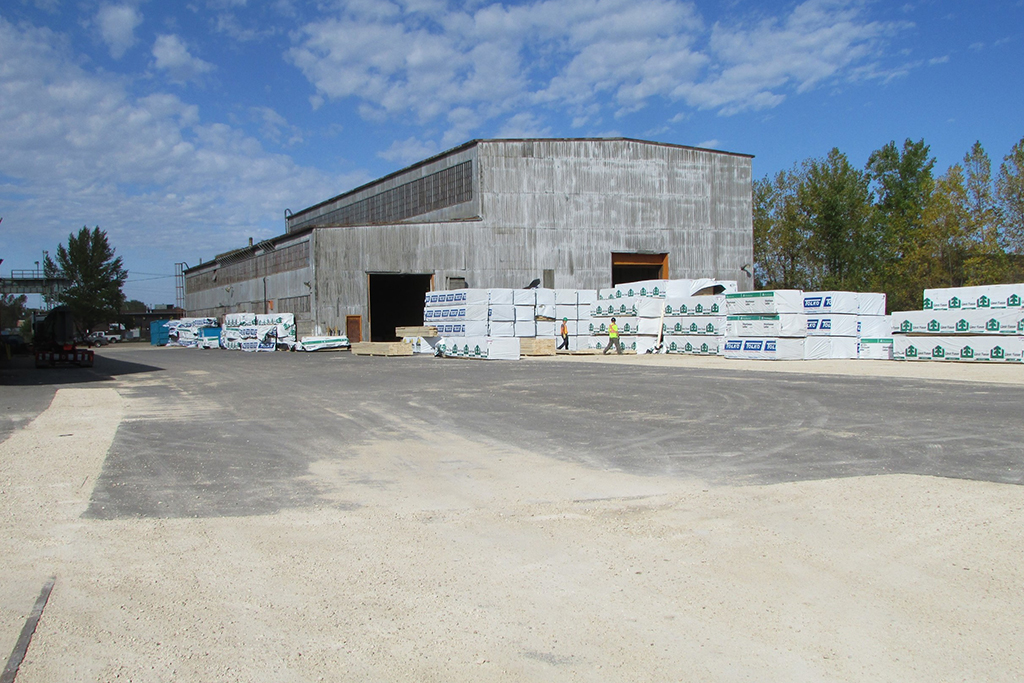
1/2
PETER CAULFIELD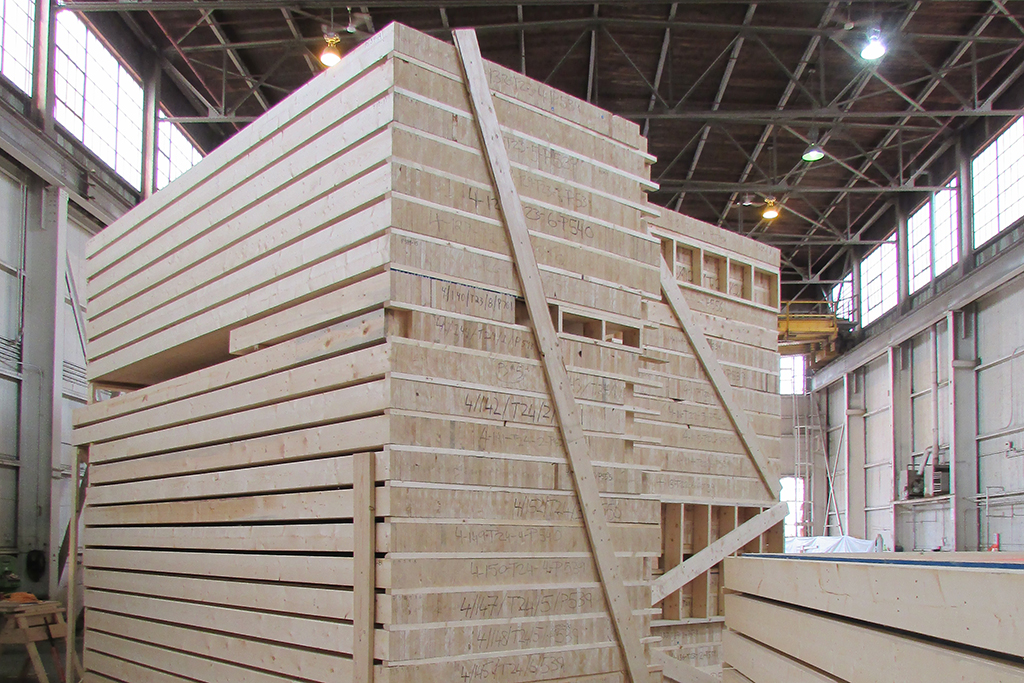
Recent Comments
comments for this post are closed