A new made-in-Alberta filter technology that incorporates aeration and swirling of contaminated water promises to change the way we purify anything from sewage to water produced by oil and gas recovery.
Inventor Peter Christou, chief executive officer of Swirltex, was a water and fuel environmental technician with the Canadian Armed Forces specializing in oil and water separation. He’d worked in the private sector with various membrane technologies but wasn’t satisfied that the technology was performing to its full potential. Essentially, membrane filters quickly become clogged with whatever they’re tasked to filter and quickly lose efficiency before they need to be scrubbed or replaced.
“Even though the physics is simple, our technique been called a new form of filtration,” says Christou. “I was playing around with membranes in my garage and the doctrine at the time was that changing the structure of the membrane was the way to get higher efficiency. I was using a tubular membrane and found that by spinning the liquids inside the membrane I could increase its efficiency.”
Through swirling, centrifugal force moves the heavier water to the outside of a standard tubular membrane where it passes through with relative ease. Lighter oil remains in the centre of the tube where it won’t clog the membrane.
Experimenting with the assistance of his children, Alexia and Paytra, Christou next achieved a breakthrough for applications involving wastewater contaminated with solids.
“The wastewater I was working with was stinking up the garage, so I ran it through a venturi to add air that would keep it fresh,” he says. “The air bubbles attached to the solids and they acted like the oil, moving to the centre of the swirling water. That was a Eureka moment. You generally need to build up a lot of pressure to move a liquid through the membrane, but the air we add takes up the same volume as water so it also requires less energy to pump.”
Swirltex first took its technology on the road in 2018 to quickly and efficiently filter the water found in community sewage lagoons. First stop: the Town of Ponoka, Alta. where Swirltex conducted a pilot program, funded by a provincial grant from the Alberta Innovates Water Innovation Program.
Ponoka operates a traditional wastewater lagoon, which relies on aeration, bacteria and evaporation to treat sewage. The treated effluent is discharged once per year. Swirltex developed a mobile proof-of-concept system, about 50 feet long, that was delivered via flatbed. Once in place, it treated the liquid found in the lagoon at a rate of 4,000 to 5,000 cubic metres per day.
As a pilot project, the treated effluent was returned to the lagoon, not used elsewhere. But the operation demonstrated that Swirltex technology could provide accelerated wastewater treatment, which could allow the lagoon to treat far higher volumes without physically expanding the facility. The Swirltex unit also worked in cold weather, allowing treatment to continue all year.
In a second project in the Town of Crossfield, Alta. the treated water from a sewage lagoon was used to irrigate fields and a local golf course.
This fall, Swirltex will be conducting its first pilot with produced water — water extracted along with oil and gas from underground reservoirs.
“We’re eager to see what the technology can do with these more challenging wastewater streams,” says Christou. “Typically, treating this water using membranes involves a lot of down time.”
Christou says he expects that the Swirltex technology would be easily adaptable to major wastewater plants.
“The reason they haven’t used these sorts of membranes is that the pumping makes their use very energy intensive,” he says. “Now that we have the energy usage down, and you don’t need as much liquid, you can do a lot more on a lot smaller footprint using less energy.”
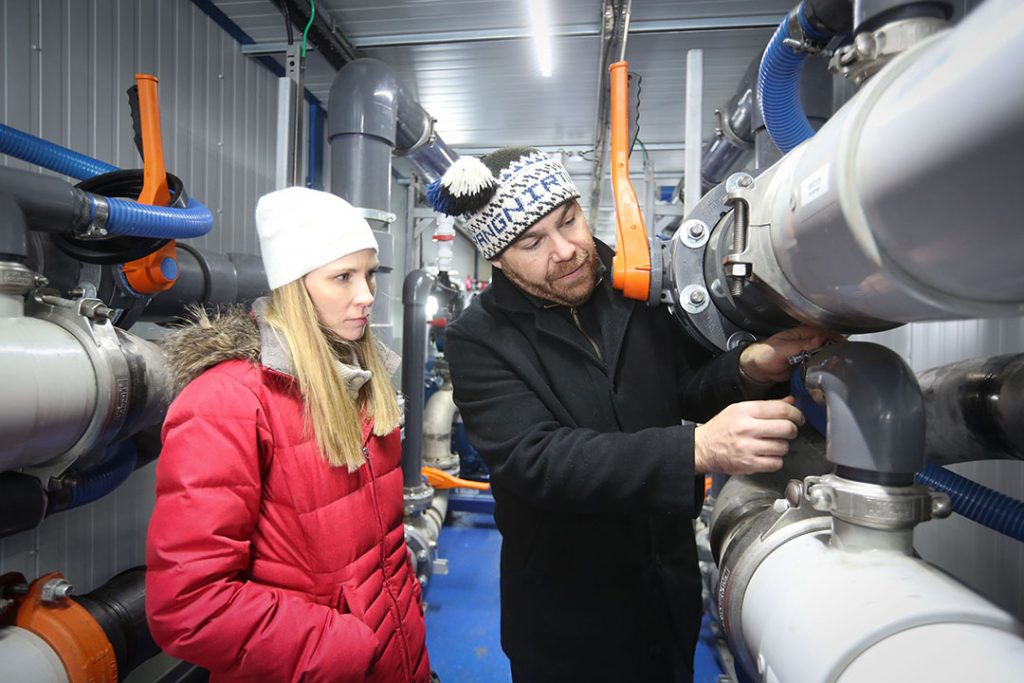
Recent Comments
comments for this post are closed