A complex concrete restoration and partial component replacement project in North Vancouver earned Vancouver Pile Driving Ltd. a Silver Award of Excellence from the Vancouver Regional Construction Association in the General Contractor under $15 million category.
The Seabus Berthing Structures and Maintenance Facility Rehabilitation project involved the restoration of the Seabus berthing structures at the north and south terminals as well as the maintenance docks.
Vancouver Pile Driving constructed the original Seabus berthing structure in the late 70s, when the company was owned by Dillingham Corporation.
The maintenance facility comprises eight concrete floats with two berths, secured by steel mooring piles and three turning dolphins.
"The floats had hollow sections and needed a lot of repair to the concrete," said Clancy Lannon, project manager for Vancouver Pile Driving.
A mechanical fueling and oiling depot on the middle float was used for oil changes and was constructed to accommodate two fuel types.
Vancouver Pile Driving built a temporary fuelling facility to service vessels during construction.
"We had to change all of that as a mechanical and electrical sub to us," said Lannon.
"The trick was getting everything apart and getting the berths open."
The north and south terminal berthing structures both comprised a three-pronged concrete pontoon structure with 88 compartments that needed extensive repair to the concrete.
"Getting the piles apart was also a trick," said Lannon.
"We couldn’t pull them because they were concrete filled. We jiggled them back and forth, put them in the graving yard and let them settle to the bottom and went to work."
The old surface material was stripped away and the concrete repaired.
An elevated timber work platform along the floats had deteriorated and needed repair.
The wood was being replaced by steel, requiring small, light members that didn’t change the freeboard on the floats too drastically.
"We redid all of the fenders," said Lannon.
"It was a challenge because if you try to go out and substitute the pieces, you can’t. The owner wanted them to match the original."
Ramsey Machine Works Ltd. fabricated custom components that are no longer available for purchase, including replacement parts for the internal and external fenders, buttress fenders and mooring piles.
The terminal and vessel exhaust ventilation also needed replacing.
The project included repairs to the dolphins —protective guides that keep the vessels from hitting the berths.
These are constructed of heavy timber and difficult to remove and take apart, said Lannon.
"We took them to the underwater graving dock to work on them," he said.
"Not knowing their condition, we had to make sure the graving dock was clean because one stone could puncture along the chines where the side meets the bottom."
Vancouver Pile Driving replaced and repaired the deteriorated components, floating them out and bringing them into the dock in sections to replace the concrete and steel as needed.
The outer fenders on the main structure were steel frame structures with timber facings hanging off of the main pontoons.
Made from exotic African ekki marine timber, the components are hard, durable and impervious to borers.
"We had to cut pieces apart that were immersed 95 per cent," said Lannon.
"We had a long lead time on them, which is good because they had to be made to the same dimensions and physical properties as the old ones."
The main pontoons required underwater and surface concrete repairs, and replacements for discontinued Lord fenders.
The biggest challenge, said Lannon, was replacing the mooring fenders for the main pontoons.
Called Seibu rubber dock fenders, these are the components that keep the terminal in place. They are 60-70 tonne pieces comprised of two sets sandwiched between steel plates.
"We had to go back to the original manufacturer and get a price to make them just like they did back then," said Lannon.
"We had to make new molds to make them."
The Seibu fenders also contained steel and wide flange members that no longer commercially exist.
Ramsay Machine Works Ltd. fabricated replacement parts.
"When we were doing that work we had to be careful the whole terminal didn’t move because the service lines had connections to shore," said Lannon.
"We had to make sure there was no damage and there are very small construction variances in getting the members out."
Vancouver Pile Driving had divers working round the clock with 12 frames under drilling and epoxying under water on the vertical, up poring holes.
"They would hit rebar and sometimes abandon a hole," he said. "The thing was keeping the terminal open and not interfering with operations."
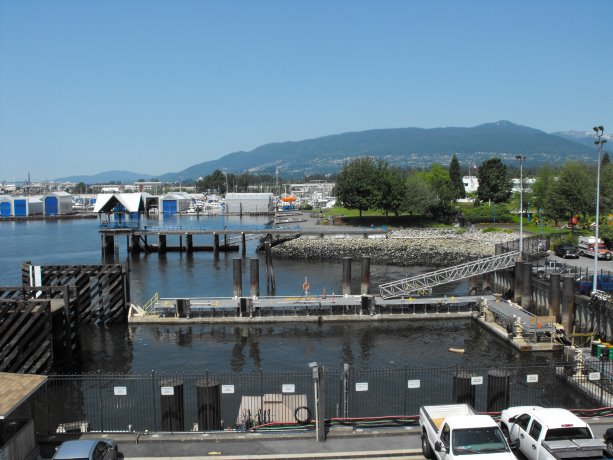
1/2
Vancouver Pile Driving Ltd.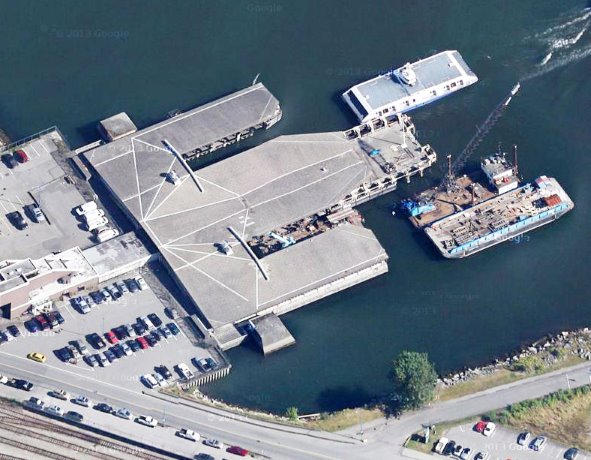
Recent Comments
comments for this post are closed