Construction projects are built one beam, one concrete slab, one steel girder at a time. With lots of planning, patience and sweat, the materials become a building. For Dave Ware, it all starts with a brick — a Lego brick.
Ware is a software analyst by day and a professional Lego builder in his spare time, crafting buildings and intricate mosaics for clients and for fun.
Like most kids, Ware played with the colourful building bricks but rekindled his fascination with them several years ago while walking through the toy aisle. He became inspired to build a pyramid and then did a mosaic of a dog.
Soon his work began getting noticed on social media. Now he is a brick artist for hire, mostly doing mosaic portraits.
But one of Ware’s biggest challenges came when he was approached several years ago by Knightsbridge Homes to build a massive replica of its planned N3 Condo project in Calgary, Alta. The 167-unit building is slated for the lot directly east of the St. Louis Hotel, which is now being renovated.
The condo project is notable as developers have chosen to not include a parkade, instead promoting a car-free lifestyle.
The ambitious Lego project took hundreds of thousands of bricks and months of careful planning so Ware enlisted the help Robin Sather, Canada’s only Lego Certified Professional, to get it done.
Knightsbridge wanted roughly a 1:24 scale model, which translates to about eight feet tall, far larger than and building Ware had constructed. But since N3 didn’t have all its final permits and Knightsbridge didn’t want to commit until that was done, the build schedule was up in the air.
This is the single biggest problem in the Lego building world. Scheduling is important as ordering thousands of bulk bricks, a luxury only afforded to a handful of builders like Sather, is a process that takes months. Once the building permits were approved, Ware and Sather got to work.
Ware used commonly known brick formulas to calculate how many bricks would be needed.
The pair ordered more than 300,000. Next he began prototyping the trickiest parts of the structure, like windows and balconies. Once those were roughed in he scaled everything else to them.
“If you can make the windows work you can probably make anything work,” Ware said.
He also ran into the problem of showing the client what the finished product may look like or cost.
Prototypes of certain sections of a structure are doable and can even be done digitally in Lego building programs. But even building in a program is a lengthy process and until you invest in the bricks and actually begin putting them together, it’s hard to say how things will work.
Ware had to learn how to work from CAD files, blueprints and architectural renderings.
“That’s super helpful because you can see how things attach,” he said. “There isn’t an instructional manual.”
Once the first floor was complete and he began building higher — the structure had to support hundreds of pounds. He used the building’s middle corridor to bear the load and constructed it out of larger, sturdier Duplo bricks. He also built a replica of the nearby historic St. Louis Hotel.
“It’s a pretty onerous process,” Ware said. “It basically consumed my life for three months.”
He and Sather stacked the bricks after work and on weekends, a painstaking process as tiny mistakes mean parts must be taken down and redone.
After more than 200,000 bricks were put together, the piece was complete. Ware and Sather broke it down into 14 chunks to transport it.
“It was a really good feeling to be done,” said Ware. “It went much better than I anticipated.”
Ware said he learned a lot from the project, including how to negotiate the construction schedule and payment with the owner and how to utilize renderings and digital models of planned structures. His work has already got him several more building projects lined up, to be built when he isn’t busy constructing mosaics.
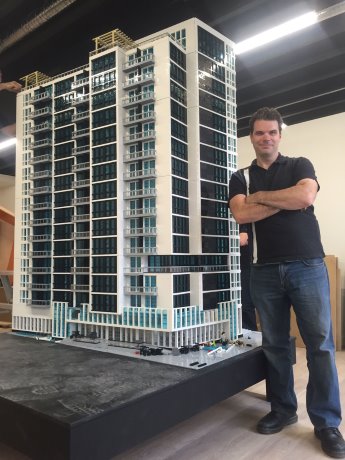
1/2
Ware poses with a replica he was commissioned to do of the N3 condo project in Calgary. It took hundreds of thousands of bricks and months to plan and build.
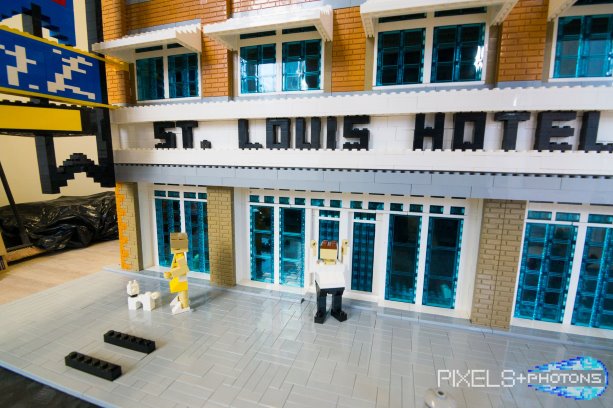
2/2
Lego figures mill about a replica of the St. Louis Hotel in downtown Calgary. The hotel was part of a massive model of the N3 Condo building project built by Calgary Lego artist Dave Ware.
Recent Comments
comments for this post are closed