On June 1, 2016 Richardson International Limited marked completing the expansion of its concrete export grain terminal in North Vancouver with the facility’s official opening.
The Winnipeg-based agriculture and food-processing company had added a $140-million, 80,000-tonne concrete storage annex to its terminal, increasing the capacity to 178,000 tonnes.
Building the storage annex was no piece of cake.
"It was a challenge to construct it on a matchbox footprint on the North Vancouver waterfront and at the same time keep the busy terminal in full operation," said Doug Petrick, senior vice-president, design and construction of the FWS Group which was the construction manager for the civil, electrical and control packages of the project.
Comprising two clusters of 52 silos, each 140 feet high, the expansion was completed in 30 months using the most recent iteration of a concrete construction technique called slip form.
"Slip form construction involves a relatively continuous pour of concrete," said George Depres, FWS chief strategy officer.
The process begins with the preparation of the foundation, in much the same way any heavy industrial foundation is built.
"Once the foundation is complete, however, the project takes a new direction," Depres said.
"A concrete forming system is constructed to rise vertically, via hydraulics, on steel jack rods that are embedded in the concrete walls of the structure."
The complete form is called the slip deck.
"In some respects, the process resembles the construction of a ship that goes on a vertical journey to the top of the structure," said Depres.
The slip deck stands about four feet high and contains open space wherever rebar and concrete is placed as the deck rises upwards.
"Imagine a very large floor with trenches running through it," said Depres.
"The four-foot depth of the floor represents the approximate volume of concrete that must be poured so that the curing concrete at the bottom of the form stays pliable enough to release from the form while fresh concrete and rebar is constantly added at the top."
Once the process starts, the deck is jacked upward at a rate of about one inch every five or six minutes, which works out to 10 inches per hour or 20 feet per day.
"The slip deck is a beehive of activity during the pour," Depres said.
"On most projects, there are two 12-hour shifts per day. The largest operations can have up to 150 personnel per shift."
Depres says that if the pour did not go around the clock, there would be cold joints in the concrete wherever it had dried before fresh concrete was added on top.
"That would negatively impact the strength, durability and appearance of the finished product," Depres said.
"Also, you would have to jack the forms free at the end of every shift to prevent the concrete from setting up and freezing the slip deck in that position."
Slip forming has been used to build concrete grain silos and elevators since the early 20th century.
"The principles have not changed much," Depres said.
"The biggest change is the size, scope and complexity of slip forming that can be undertaken today."
Concrete prairie grain terminals that are built with slip forming are about 130 feet high.
"In concrete grain elevators on the prairie and at ports such as Vancouver, you can see how the technology has evolved over time," Depres said.
"The size of today’s facilities dwarf most of the facilities constructed in the past. In addition, the form work that is needed today is much more complex."
Concrete is the material of choice for most grain elevators that are built in Canada today, says Brian Olson, Richardson’s assistant vice-president of engineering services.
"Concrete elevators are superior in every way to wood," said Olson.
"They’re stronger and they last longer, too."
Richardson operates 59 grain elevators across the four western provinces.
"Of that number, a small handful are wood; the rest are concrete," Olson said.
The transition from wood to concrete elevators began in earnest in about 1990, as the grain industry consolidated and increased in scale. The change reduced the need for many small elevators scattered over the prairies.
"The total number of elevators is way down," Olson said.
"Twenty-five years ago there were about 1,500 in western Canada. Today there are only 326."
The relatively low-capacity wooden elevators were replaced by higher-capacity concrete ones, which are able to load a long unit train of grain cars quickly and efficiently.
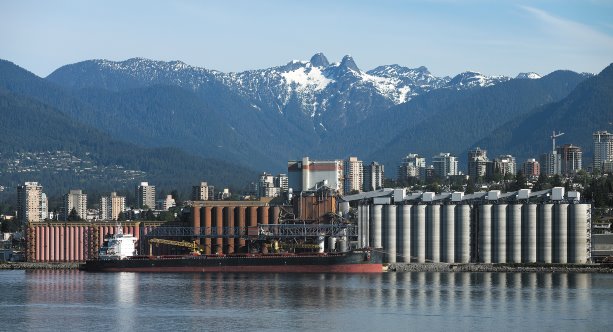
1/2
The use of concrete slip form construction was integral to expanding the Richardson International Limited concrete grain export terminal.
Photo: Submitted Photo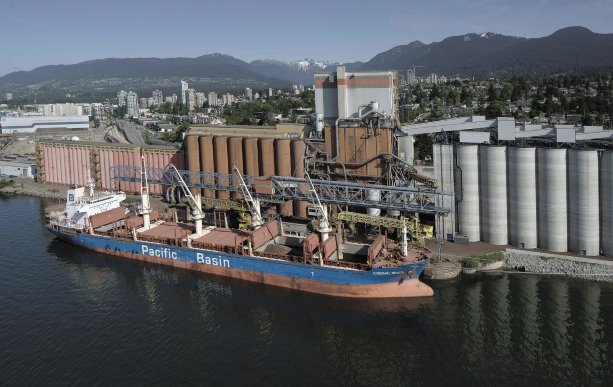
2/2
Comprising of two clusters of 52 silos
Recent Comments
comments for this post are closed