Burnaby-based Gisborne Industrial Construction Ltd. recently completed construction of a new permanent secondary crusher at the Copper Mountain Mine near Princeton in southern British Columbia.
"The crusher is one of the biggest in Western Canada," said Gisborne president and chief operating officer Ron Spironello. "Its power and sheer size are unique."
The owner of the project, Copper Mountain Mining Corporation of Vancouver, is now putting the crusher, which takes big rocks from the mine and grinds them into smaller ones, through the commissioning process.
Spironello is not exaggerating.
The FLSmidth Crusher Raptor XL 2000 comes with a 2,500-horsepower motor and can process between 1,000 and 3,000 tonnes of ore per hour.
The machinery is not just powerful, but extremely big, standing 10 storeys high.
The lower main frame is the largest single piece of the machine. It weighs a little more than 100 tonnes and is almost six metres in diameter. It is so large that it could not be handled by the Port of Vancouver when it was shipped from its point of origin in Europe.
The equipment took a long and involved journey to get from where it was manufactured to its destination in the mountains of southern B.C.
It was shipped from Bucharest, Romania to the Port of Halifax, where it was put on a train and taken to Kamloops.
It was unloaded by cranes from its flatcar and loaded onto a truck.
It took four nights to transport the equipment the 200 kilometres from Kamloops to the mine site.
The equipment’s slow trip to the mine site required a detailed traffic management program, in order to minimize traffic disruptions along the route.
The journey had to take place between midnight and five in the morning, while the highway from the rail yard to the mine site had to be blocked off in sections.
Also, all of the bridges being crossed needed to be re-engineered to ensure they wouldn’t buckle under the weight of the equipment.
The convoy’s progress was extremely slow.
It traveled at a rate of only 10 kilometres per hour (an average person walks at a rate of six to seven kilometres per hour).
Once it reached the mine site, the crusher was put in place with a 275-tonne crane, which the mining corporation bought when the mine was built in 2010.
Gisborne acted as the general works contractor on the job.
The company was responsible for detailed earthworks, concrete, piping, mechanical installation, electrical and instrumentation.
Spironello said the construction part of the project included a number of challenges.
"First, there was the climate to contend with," he said.
"When concrete was poured in the winter, it had to be heated."
Another challenge was getting equipment and manpower to the mine site on time.
"Rigorous pre-planning was necessary," Spironello said.
The added safety concerns that come with mining projects compared to non-mining projects also had to be contended with.
"The rules for mine construction are slightly different from non-mine construction," Spironello said.
"Health and safety on a mine site falls under the jurisdiction of the Health and Reclamation Code for Mines in B.C. This often refers back to the Occupational Health and Safety regulations, but there are some unique safety items."
The mine produces copper concentrate for smelters in Japan.
Copper Mountain Mining chief financial officer Rod Shier said the secondary crusher will solve a problem that has plagued the mine since it was commissioned three years ago.
"The mine has not been able to consistently operate at design output levels ( 35,000 tonnes per day) due to the toughness of the ore," he said.
"The main bottle neck was in the SAG (semi-autogenous grinding) mill, which has had difficulty processing the larger pieces of ore.
"Installation of the secondary crusher will take care of this problem."
Ore from the mine is put into the primary crusher, which crushes the rock into smaller stones that are less than 5.5 inches in diameter.
These stones are then transported by conveyor belt to the secondary crusher, where they are reduced in size to less than two inches in diameter.
After that, the ore is conveyed to the SAG mill for further crushing and grinding.
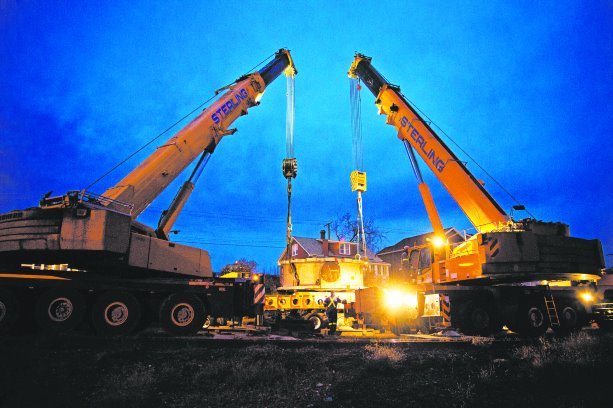
1/2
Copper Mountain Mining Corporation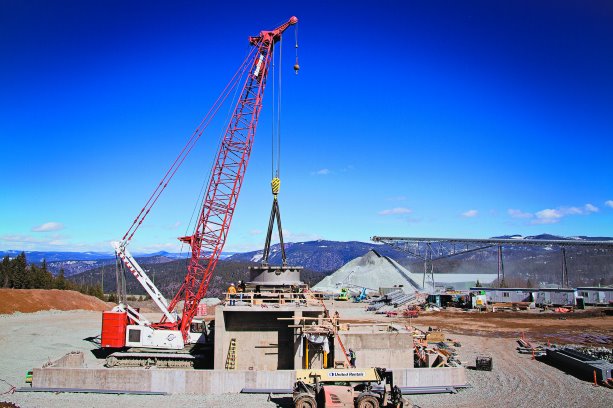
Recent Comments
comments for this post are closed