When the $126 million University of British Columbia (UBC) Orchard Commons complex is complete in mid-2016, the structure will showcase not just sustainability but will combine old and new methods of pre-fabrication. The complex consists of a north and south residential tower, both accommodating a total of 1,038 students.
The UBC Vantage College will have 23 classrooms for international students in a four-storey podium at the bottom of the south tower, with common areas connecting the two towers that include resident support services, a 450-seat dining hall, activity area, day care and multi-use rooms.
Nail laminated timbers (NLT) is a mass timber construction method that nails the wider faces of two inch (2x4s, 2x6s, 2x8s, 2x10s, and 2x12s) dimensional lumber together to achieve panel thickness. It is being used as roof panels in the complex’s common area and also as stairs in the towers, where every three floors flow into a central lounge.
"This use of NLT is quite old," said Lucas Epp, StructureCraft’s manager of engineering.
He added that these panels can be found in some of the century-old timber structures in Vancouver’s Gastown. They can be used on floors, decks and roofs.
StructureCraft produced the NLT panels that were used in the roof between glulam beams that spans the open common areas and the NLT for the stairs in the towers.
It also fabricated the large glulam beams to the client’s specifications to support the roof.
Six large glulam beams designed by StructureCraft were delivered to site, where the company erected them using a tower crane.
The six beams measured 315 mm in width, 1,060 mm in depth and were 21 metres long.
However, they are not the longest beams that StructureCraft has forged.
"They are pretty long," said Epp, adding they fall short of the 40-metre glulam beams supplied for the Bow River Bridge.
As well as the large span beams, StructureCraft supplied 30 smaller glulam beams that were eight meters in length and 460 mm in depth and 175 mm width.
Glotman Simpson’s project engineer Neil Wilson said the large glulam beams facilitate the design for a large open area commons space.
"The reason that we were able to do the span is because it was a roof and there were no floors loaded on it," he said.
Other engineering challenges included merging features of the structure.
The south tower sits over the dining hall and Vantage College areas, and therefore a series of large transfer beams had to be installed on level three.
"Designing these safely and maintaining the architectural intent for clear head-rooms was a challenge," said Wilson.
The Vantage College atrium was also a challenge as it features reinforced concrete bridges that span 12 metres.
The bridges have two 750 mm deep beams on either side so that services can run between.
The beams also support the steel cantilevered stairs that connect the bridges.
Marcin Szenowicz, Stuart Olson Construction’s senior project manager, said the project features a variety of building methods and materials.
This includes 20,000 cubic metres of cast-in-place concrete and hundreds of pre-cast insulated concrete panels, two curtain wall systems (stick and unitized) and wood composition components (glulam and NLT).
But, the construction focus has been on manufacturing the components as much as possible off site.
"We reduce the risk of poor quality," he said, adding that off-site production isn’t impacted by inclement weather.
The project used 1,100 precast insulated concrete panels on the towers to enhance insulation plus triple glazing on windows to minimize heat loss and gain.
The building is looking to achieve LEED Gold certification and will connect to UBC’s district energy system.
"A lot of towers today are not fully glazed – the glass does not have the R-value needed to prevent heat loss," said Szenowicz, adding this puts a tremendous demand on heating and cooling system.
The insulated panels supplied by Architectural Precast Systems Ltd. in Langley have a three-inch structural concrete wythe, insulation in the core and a three-inch facade or architectural wythe of white concrete to form the exterior cladding.
The colour helps to reflect sunlight.
The 1,100 insulated panels, which have the cladding face sandblasted, create a unique pattern with 18 different panel forms.
Computer-generated sequencing placed the panels on the exterior providing an appearance that eliminates a utilitarian or boxy look often associated with precast.
Perkins+Will lead architect Derek Newby said that creating an interesting facade for the tower exteriors was a client criteria.
"The precast concrete used for the towers is really innovative," said Newby. "We took something that came with a lot of baggage and have tried to give it a more organic character."
Newby said that other challenges associated with the project included coordinating the window installations and precast panel installation crews.
"There is always a lot of alignment and connections to be made and the two have to work together. There was a lot of collaboration," he said.
The design and documentation phase of the project was achieved under a tight UBC time line of a year, he said.
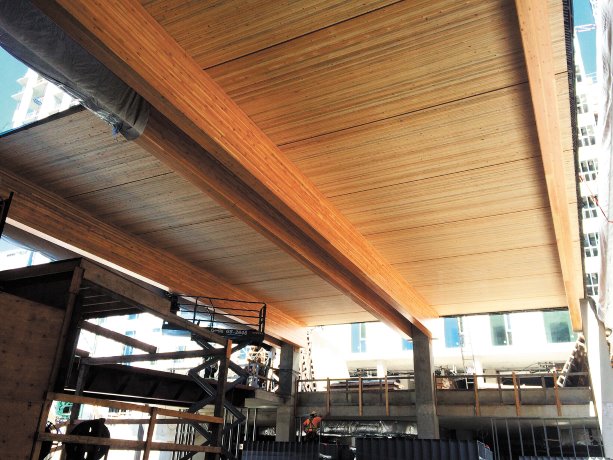
1/2
Nail laminated timbers have been placed between glulam beams for the UBC Orchard Commons project in Vancouver, B.C.
Photo: University of British Columbia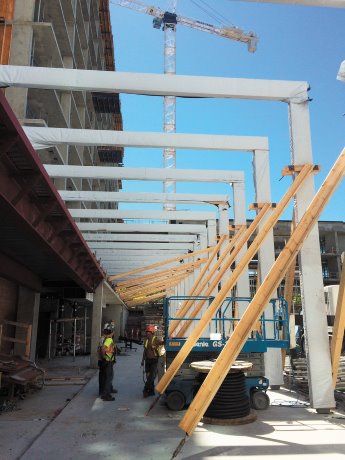
Recent Comments
comments for this post are closed