A Vancouver construction company is moving to a new house and doubling down on its core competency.
Lucas Epp, the head of engineering for StructureCraft Builders, gave highlights of the design and construction of the StructureCraft dowel laminated timber (DLT) plant, a wood-based industrial building, at the recent Wood Solutions Conference in downtown Vancouver.
StructureCraft recently entered the mass timber market, Epp said, and applied the firm’s timber structural engineering approach to complex wood projects towards mass timber use.
After the recent upsurge in wood construction, they decided to build their own plant and relocate to Abbotsford. The only choice, given their reputation for wood construction, was to use the material for their own headquarters, he said.
“Our idea was to take the idea of tilt-up concrete and apply it to wood,” Epp said.
The way to undertake this approach, he said, was to create a system that modularized roof panels and wall systems which resulted in rapid onsite construction. Tilt-up concrete is cost effective and the only way for timber to compete was to modularize.
“The building is essentially a big box,” he said.
Adopting the tilt-up model, Epp said, allowed them to put up the building in five days. The building was also delivered for the same cost as a tilt-up project.
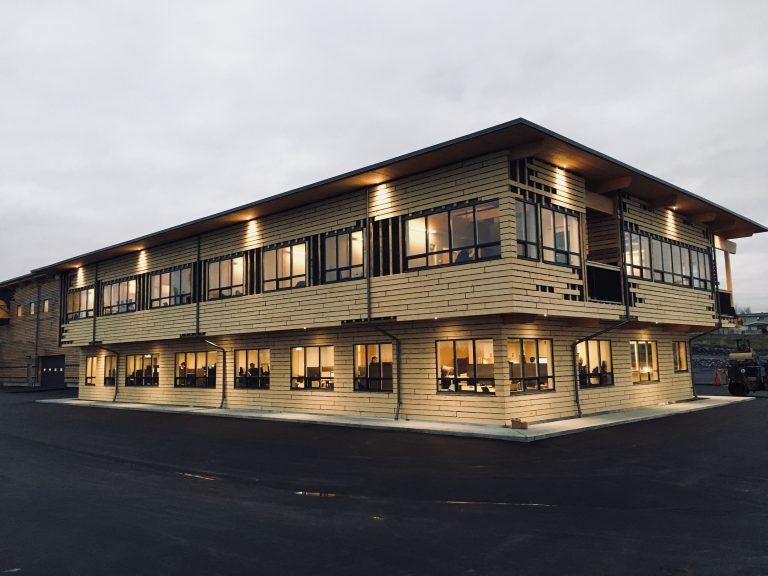
Wall panels spanned over 32 feet and the roof panels were double glulam beams prefabricated onsite. Plywood sheeting on top creates a structural diaphragm on the roof, Epp explained.
“This building has no internal bracing,” he said. “The panels on the roof act as a large beam.”
Pre-fabricated wood panels created the “structural diaphragm of the building,” he said, and once onsite the same tilt shores used in concrete tilt-up projects were used to hold the panels in place. Brackets were built right into the wood.
One of the big challenges for this system was the openings, Epp said, since large spaces were needed for trucks to enter and leave the building.
“The amazing thing is that these panels were installed with three guys, two on the panels and one on the ground,” Epp said.
Panels were being built onsite and heavy snow last winter caused disruption, but “despite all the snow we stayed on schedule. Tilt-up concrete would have been dead in the water. You can’t cast concrete at that temperature,” Epp claimed.
There are two bays in the building, one for assembling dowel laminated timber and the other for bespoke projects, Epp said.
The two-storey, 5,000-square-foot office section of the structure is made with mass timber. The office building is structurally decoupled from the manufacturing facility, both to address different seismic needs but also to disconnect the office from the loud acoustics of the warehouse section.
Putting wood fibers between gaps in boards in mass timber panels helped to reduce noise, he added. Acoustic mats were also used on the floors.
DLT was “the whole reason we we’re building this plant, to manufacture DLT and create a new revenue stream for the company,” he said.
Automation was implemented because after manufacturing a substantial amount of nail laminated timber (NLT) for the T3 wood project in Minneapolis, “we never wanted to build NLT by hand again.”
But it is difficult to automate NLT manufacturing because CNC machines and nails don’t mix, Epp said.
However, DLT is a much more machine-friendly material and dovetails with British Columbia’s drive for sustainability in construction.
The main advantages of DLT are that it is a 100 per cent wood product, does not have off-gassing and is CNC-friendly, Epp stated.
However, it is less dimensionally stable and is more susceptible to moisture during construction. Once sealed and complete, moisture is less of a concern, Epp added.
Recent Comments