Engineers continue to expand the size of loads supported by wire rope, from tension cables on bridges, to payloads lifted by cranes on construction sites, or for equipment used in the gas and oil industry. However, each time wire rope becomes stronger, someone has to develop a new wire rope test bed to test that rope for loads of millions of pounds.
The Chant Engineering Company in New Britain, Pa. is the largest of a handful of companies that design and build wire rope test beds for the world market. "We provide testing equipment for wire ropes, slings and anything north or south of the hook," says Patrick Shire, vice-president of sales and marketing for Chant Engineering.
"We generally supply the equipment to rigging shops who supply the wire rope. Our most popular units are standalone horizontal models, generally about 40 feet long, that you can drop onto a shop floor. They’re built of steel and steel I-beams and powered by electrically driven hydraulic cylinders that apply a tensile force of up to 1.3-million lbs. Each unit is operated by proprietary software to maintain accurate control and calibration."
Test beds are generally used for three purposes: non-destructive testing of the tensile strength of wire rope; break testing, to determine the load a wire rope can support before it fails; and pre-tensioning of wire rope used in construction, to ensure the cable doesn’t stretch following installation.
"If we’re testing a sling rated for a working load of 100,000 lbs., it has to be proof tested to two times the working load, with a typical design factor of five to one — 500,000 lbs.," says Shire.
"You could determine the design load through break testing and the working load limit of wire rope that’s already in service through proof testing." Test beds must also be calibrated once a year by Chant personnel.
Chant sends testing personnel to locations as diverse as Vietnam, South America and Equatorial Guinea.
Chant has also upgraded test beds as many as 70 years old to meet modern standards.
"The old models that used pressure transducers are no longer recognized by ASTM (an international standards group)," says Shire. "In some cases they still have the big old-fashioned dial and arrow."
"We upgrade them to use electronic load cells and bring them into compliance." Shire notes that the market for test beds is heading in one direction — bigger, longer and more powerful. "The oil and gas industry in particular is tending toward heavier equipment and heavier loads," he says. "Everything is now an engineered lift."
Chant’s most powerful test bed to date is a horizontal unit built in Houston for Bishop Lifting Products Inc. The device measures 365 feet long and can exert a tensile strength of 3.3-million lbs. The diverse machine can also test the loads on spreader bars and crane blocks.
"Our regular horizontal units don’t have to be bolted to the shop floor, but for units rated as high as this one a foundation for the steel structure comes into play," says Shire.
"They had to excavate eight feet down to pour the concrete and every 10 to 20 feet they drilled 14 feet down to put in six-foot solid concrete footers."
Designing a test bed for break testing requires personnel to be protected from the explosive force of the destruction of wire rope of massive diameter. In this case Chant designed a system where the control room is located on the second floor of an adjacent building, with the room clad in quarter-inch steel plate and half-inch steel plated flooring.
"When a large steel wire rope breaks, it sounds like an explosion and generates an electrical force as the wires shoot sparks," says Shire. "It’s pretty spectacular."
While the Houston project represented a record for Chant, 2010 was a long time ago in engineering terms.
"We’re in talks to build a test bed that would eclipse the last record," says Shire. "If we take on that contract it will be the largest test bed ever built."
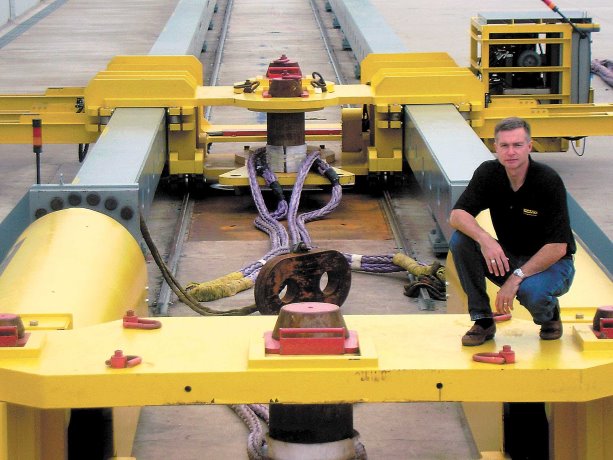
Phil Chant, vice-president at Chant Engineering, kneels next to a 3.3-million pound wire rope test bed built for Bishop Lifting Products Inc. in Houston.
Photo: Chant Engineering"
Recent Comments
comments for this post are closed