Meta’s announcement in September of its new investment in low-carbon concrete production potentially opens a new era of development.
Meta has agreed to assist CarbonBuilt to further expand production of Reversa®, a product designed to replace traditional Portland cement with a low-cost alternate.
CarbonBuilt was set up four years ago and is today based in Torrance, Calif. It will use the Meta investment to upgrade its new concrete production facilities in Alabama and Arizona.
Reversa® is made from a widely-available low-carbon material that hardens after chemically reacting with CO2. The company says the binder enables concrete producers to reduce the carbon footprint of their products by an average of 70 per cent, with no compromise to product cost, performance or plant operations. This process strengthens the concrete blocks while permanently storing the CO2 in the blocks, thereby diverting it from the atmosphere.
“Our global infrastructure is what enables us to deliver the products and services that billions of people use around the world, and data centres play a big role in that,” John DeAngelis, head of clean technology innovation at Meta, said during Climate Week in New York City. “But concrete as well as other key hard to abate industries represent a big chunk of the embodied missions associated with the data centre infrastructure.”
CarbonBuilt says its low-carbon solutions are delivered through regional partnerships with existing concrete manufacturers. This ensures availability, consistency and cost competitiveness, widely regarded as keys to commercial success in the new era of concrete and cement alternatives.
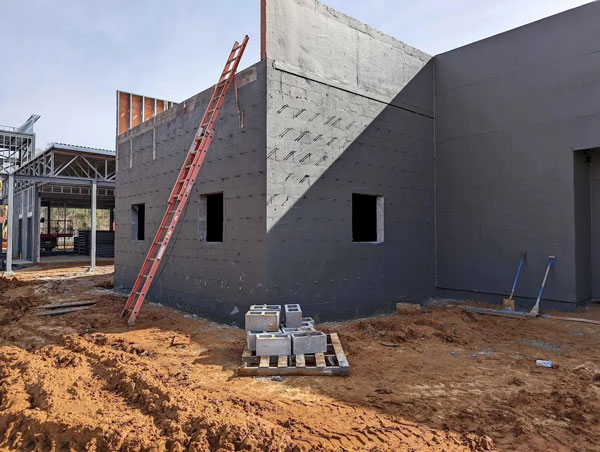
Meta’s announcement is coupled with a White House announcement concerning commitments from some of the largest suppliers and users of concrete to invest in low-carbon alternatives.
Meta has also joined with Amazon Web Services (AWS), Google and Microsoft in The Open Compute Project Foundation, a demonstration project that tested ultra-low carbon concrete solutions and will publish its results soon. Microsoft and AWS are also making substantial low-carbon material investments.
Meanwhile, a number of large U.S. construction companies such as Clark Pacific and Turner Construction have committed to low-carbon concrete demonstration projects.
Even more major investments in low-carbon concrete alternatives are coming into view, the result of some interesting partnerships.
Among these is the recent $85 million infusion into Silicon Valley-based Fortera made by five investors including venture financiers Khosla Ventures and Temasek.
Fortera’s product is called ReCarb, a process that captures CO2 emissions directly from current cement production and converts it to ready-to-use low-carbon cement. The new investment paves the way for a large-scale commercial launch.
Fortera expects full-scale ReCarb plants will mineralize 165,000 tons of industrial carbon dioxide and produce approximately 375,000 tons of low-carbon cement annually.
“Due to the scale of the industry, we won’t have an impact on emissions unless we have an economic pathway to expand globally,” Ryan Gilliam, CEO and co-founder of Fortera said in a media release. “With the launch of our first plant and the close of this funding round, we’re entering into the next phase of our development as a commercial project company to accelerate low-to zero-carbon cement deployment.”
Fortera’s “next phase” is being made possible due to global material giant Saint-Gobain standing alongside the venture capitalists.
“Our investment in Fortera aligns with Saint-Gobain’s priority toward the decarbonization of industries and our commitment of working with startups that are moving the world forward with sustainable innovations,” said Basma Kharrat, vice-president of external venturing at Saint-Gobain.
Meanwhile, Saint-Gobain material competitors on the world stage, Holcim and CRH, have announced a $75 million investment in Sublime Systems, a spinout development from MIT.
“Sublime’s fully electrified, ‘true-zero’ approach avoids the industry’s legacy fossil-fuelled kilns and limestone feedstock,” Holcim says.” Sublime’s electrochemical process instead extracts reactive calcium and silicates from an abundance of raw materials at ambient temperature, to make ASTM C1157-compliant Sublime CementTM, a drop-in replacement for ordinary Portland cement in concrete.”
The partnership will advance Sublime’s first commercial manufacturing facility in Massachusetts giving Holcim a large share of Sublime CementTM.
John Bleasby is a freelance writer. Send comments and Inside Innovation column ideas to editor@dailycommercialnews.com.
Recent Comments