After four years of construction, two distinctive looking 62-storey towers in Mississauga, Ont. were officially “topped off” in early September by the developers and Mayor Bonnie Crombie.
M1 and M2 are the first towers of Rogers Real Estate Development Limited and Urban Capital’s M City, a multi-phase, master-planned community located on Burnhamthorpe Road West and Confederation Parkway.
Upon completion, it will be an eight-tower, 15-acre, 4.3-million-square-foot development. The site will also bring over two acres of new parkland to the community with dedicated connections to the Mary Fix multi-use trail and neighbouring parks.
Now the tallest towers in the city, although eventually to be eclipsed by its sister building, the M3, the towers are distinguished by their unusual appearance.
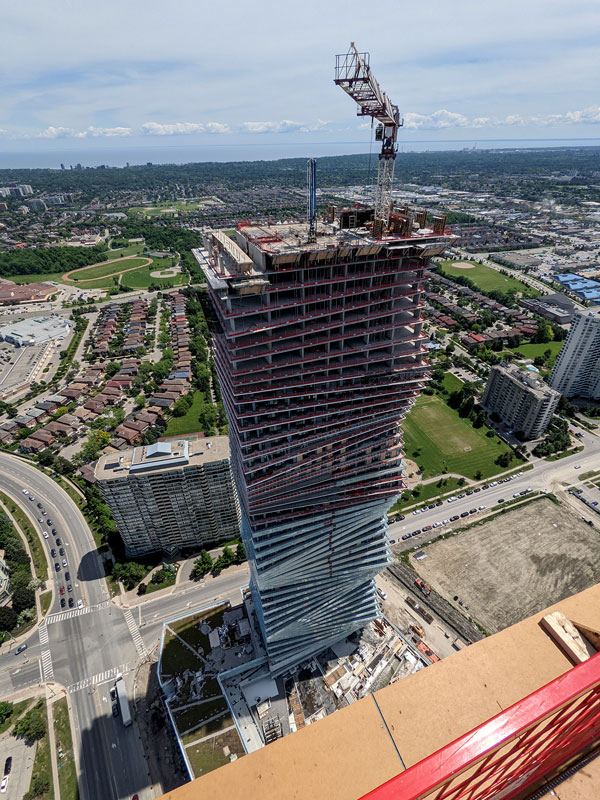
EllisDon is the construction manager overseeing the simultaneous construction of the two “twisted” towers, which were designed by Core Architects, with structural design by RJC Engineers. Each floor twists back and forth up the height of the tower in a pattern consisting of seven different floor plates.
“The developer wanted something memorable and eye-catching and so did the City of Mississauga,” says Brian Laye, a partner with Core Architects.
Initiated after several earlier concepts had been evaluated, the design development stage took about a year-and-a-half to perfect and required input from the client, contractor and the building envelope consultant, he says.
As just one example of the numerous elements that had to be evaluated, Laye points out each floor has its own roof and soffit condition.
With its unusual geometric design and construction, the towers have been generating a lot of “buzz” and social media commentary, especially after they began rising above their respective podiums, says RJC project engineer Daniel Snodgrass.
Designing the towers from both an architectural and structural perspective meant taking into account not just the external wind and seismic forces any tall building is vulnerable to, but also the internal ones, says Snodgrass.
“While the twisting doesn’t cause a significant change in the building’s overall overturning load demand — such as wind or a tilted tower imposes, it does create large loads that want to ‘wring’ out the structure.”
To counter that risk, RJC designed a centrally positioned reinforced concrete coupled core system with flange walls.
Walking or alternating columns were installed to provide for easier rebar placement and more straightforward formwork while not compromising the suite layouts, he says.
“Twisted towers are not unusual, but they are rare,” says Snodgrass.
An intensive all-encompassing process was invested into the design to ensure the towers were not overly complicated to build for the construction manager and especially its two concrete forming subcontractors, one for each tower.
“The crews caught on very quickly (to the design),” says Snodgrass.
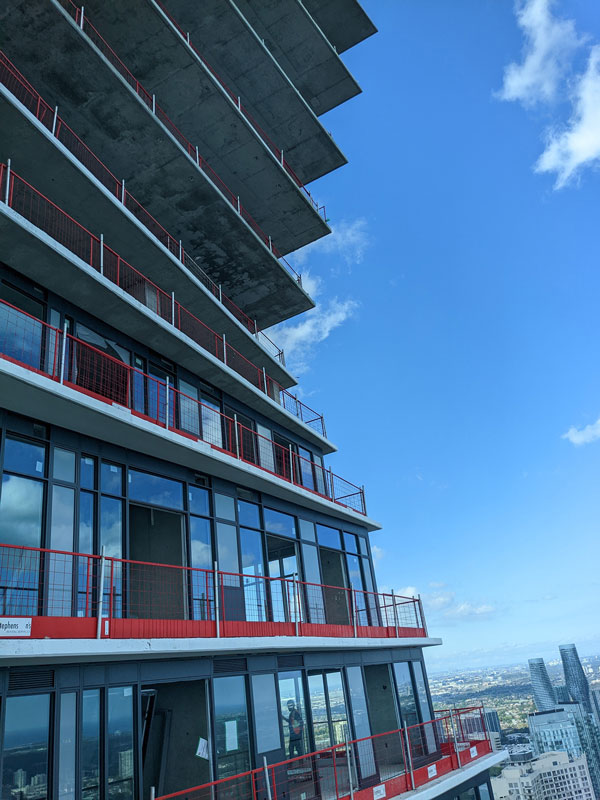
A conventional fly form system was used and the concrete was pumped to each floor, a process that did require some planning and set up time, he explains.
The fly forms had to take into account the undulating floor plates and, due to the shifting floor plates, the reinforcing steel installations of the walking columns required precise placement to ensure consistent development of the steel from level to level, says EllisDon senior project manager Adam KleinHerenbrink.
Innocon is the concrete supplier and Res Form Group is the concrete formwork subcontractor.
Approximately 53,000 cubic metres of concrete was placed in the M1, whereas the volume in M2 is closer to 56,000 cubic metres, says KleinHerenbrink.
Apart from the towers’ obvious design challenges, the more unpredictable ones were pandemic related, such as trade contractor labour impacts and retention issues and supply chain disruptions, he says.
At the topping off ceremony, which also marked the groundbreaking of the M4 tower, Rogers Private Companies president and treasurer John Anderton described the event as the realization of its vision of creating a “world-class community” in the city.
“We have an unwavering belief in this city and look forward to continuing the momentum from these milestones, cementing M City as a catalyst for the evolution of Mississauga.”
Recent Comments
comments for this post are closed