Recent provisions under the National Building Code (NBC) pave the way for tall wood structures up to 12 storeys in Ontario but advice from one experienced builder on the West Coast is that these buildings present plenty of hurdles for the unprepared.
While construction times can be shorter with mass timber than concrete and steel, the time savings is lost without a framework of preconstruction, procurement and scheduling laid out ahead of time to minimize disruptions during construction.
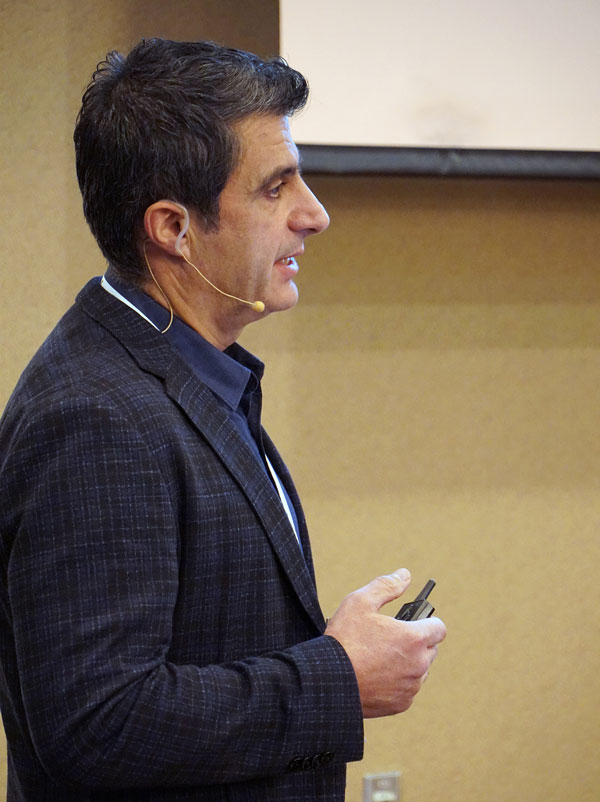
“It has to go smoothly otherwise you lose all the advantages you have been calculating in your costing,” said Mehrdad Jahangiri, a partner with Vancouver-based Aspect Structural Engineers.
He gave a seminar at the Toronto Wood Solutions Conference recently on Aspect’s experience with Canada’s first tall wood mass timber residence known as Tallwood 1 in Langford, a municipality within Greater Victoria.
Constructed under the NBC’s new Encapsulated Mass Timber Construction (EMTC) provisions, Tallwood 1 contains 11 mass timber storeys on a concrete transfer slab. The tower consists of cross-laminated panels and glued laminated timber, also known as glulam, columns.
It was built for roughly $300 a square foot above grade. Factor in the two subfloors and that number drops to about $265 a foot, he told the packed room at the Paramount Event Space in Woodbridge.
“I don’t think you can build a spec home for that price right now.”
But Jahangiri said meeting schedules and budgets isn’t easy.
He said Design Build Services, the Langford tower’s developer, recommends developers get experience with smaller mass timber projects before taking on a 12-storey mass timber building.
Tall wood buildings can be built for about five per cent less than six-storey mass timber structures but to meet budget requires a speedy assembly and erection, according to the developer, which has built a number of midrise mass timber buildings prior to Tallwood 1, said Jahangiri.
“You need to be dialed in,” he told the seminar audience, adding contractors and their subs need trained crews in the medium.
The Victoria project was completed in 26 months with only the penthouse showing exposed mass timber on the exterior, in accordance with the EMTC provisions.
Seismic detailing was one of the challenges at Langford.
Jahangiri said the project required specially engineered eccentrically braced frames (EBF). In less earthquake prone areas such as Greater Toronto the lighter eccentrically braced systems can be specified.
“On the West Coast we spend a lot of money on seismic detailing that you guys (Toronto) don’t have to do.”
Tallwood 1 was under development when the pandemic hit, throwing wrinkles in the original design. The specified curtainwall made in Texas was unavailable during the border lockdown and was replaced by a façade that included stick frame and plywood.
“We were forced to scaffold the entire building to install the (replacement) panels,” he explained.
Under the EMTC provisions, a number of 12-storey mass timber projects are in various proposal submittals and approval stages in the GTA.
Aspect Structural Engineers opened an office in Toronto in 2019 in response to the growing mass timber market.
Eva Chau, an associate at the firm, said building robustness into tall wood designs is paramount but Canadian building codes “don’t do a great job explaining how this can be done so we usually turn to the European code to provide more guidance.”
She said another important design consideration is connections.
The selection on the market varies but some connectors are a better fit for some mass timber towers than others.
“The risk of not knowing upfront is that you might have code-compliant (wood) members that work but once you do the connection design you can’t fit the connection into the member.”
Chau said specifying certain connections could require an increase in member sizes, which is “never good for your client.”
She pointed out while mass timber costs more per square foot than concrete, the difference can be made up through “little nuances, or you can take advantage of the speed of construction.”
In partnership with the Canadian Wood Council, Aspect Structural has conducted a cost comparison study between an existing concrete tower and a hybrid mass timber structure comprised of cross-laminated panels and a steel lateral braced system. The study’s conclusions are expected to be released soon.
Recent Comments
comments for this post are closed