Cenovus Energy operates a module-building yard in Nisku, Alberta, which allows the company to implement a unique strategy for the construction of their oilsands production facilities near Fort McMurray.
Cenovus Energy operates a module-building yard in Nisku, Alberta, which allows the company to implement a unique strategy for the construction of their oilsands production facilities near Fort McMurray.
“The unique strategy is to control the variability you get when you go to multiple third-party shops that often find it difficult to make changes in the sequence and timing of pipe racks,” said Gino Jimenez, Cenovus group lead for construction at Christina Lake.
“We can control our own destiny and have the flexibility to speed up or slow down production depending on how construction is going. We like to be ahead of the game and ready before the field needs the modular units.”
At the Nisku yard, Cenovus is able to avoid problems associated with using outside suppliers, by building the modular units for its Christina Lake and Foster Creek oilsands plants.
“We bring structural members that are fabricated by six different third-party steel shops into the yard,” said Jimenez.
“This is the raw material for our process. Once we get the structural members, we assemble them together into pipe racks. Next, the guys use engineering drawings to determine where the spool pieces or pipes are attached to the pipe rack.”
The structural members come into a staging area and then the fabrication work is distributed to mechanical contractors at 45 work stations spread out across the 31 acre site. Each work station builds an individual pipe rack.
“After the structure and the pipe spools are erected, the pipes are winterized or glycol traced, so services in pipes don’t freeze on site,” said Jimenez.
“Hot glycol is run in tubing outside the pipe to maintain fluid inside the pipe. Then, the electrical systems are traced.”
The modular yard has 27,000 sq. ft. of warm storage space, which allows the staff to stock up on project consumables, such as valves, electrical cable and other stock for production.
The large number of modules being built in the yard allows the company to avoid delays, due to a lack of stock.
Production at the Nisku yard has increased from 100 modules in 2009 to an estimated 170 modules in 2011.
After completion, each module goes through a quality assurance process that verifies dimensions, checks for defects and makes sure everything is bolted together properly.
The units are transported by truck to the construction site and are a maximum size of 30 feet high, 24 feet wide and a length of 120 feet or more.
“When the module leaves the yard it is identified by a letter for delivery and construction on the site,” said Jimenez.
“The module is loaded on the truck in the same orientation that is needed by field staff, so it can be dropped off on site in one lift.”
Cenovus also works as its own general contractor on construction at the Christina Lake and Foster Creek oilsands projects.
This approach allows the company to learn from their own experiences in all areas including shipping, fabrication, construction in the field, support services, logistics, procurement and contract labour.
“When construction on certain parts of the plant fall behind, we can slow down the fabrication of some sets and accelerate others to ensure deliveries are still made on time,” said Jimenez.
“We can do this seamlessly because we control production and shipping, as well as construction on site.”
This integrated approach to the construction of oilsands facilities was developed by Cenovus a few years ago using a smaller version of the current Nisku yard.
“In 2007, we tested the concept of owning our own fabrication yard on the Foster Creek project phase D and E,” he said.
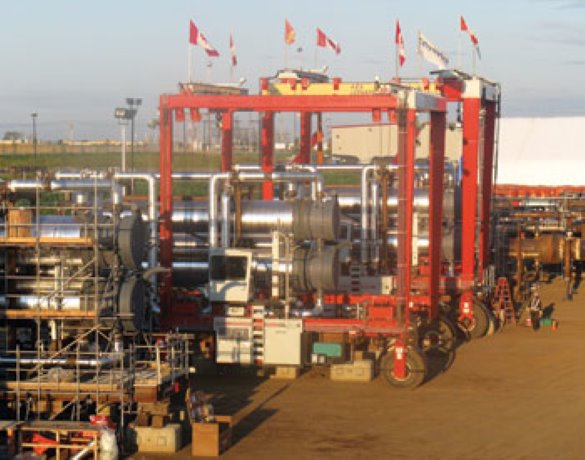
Cenovus Energy module-building yard in Nisku, Alberta
Recent Comments
comments for this post are closed