There should be fewer lingering odours from Saskatoon’s waste water treatment plant in the future. The City of Saskatoon has awarded an $8.2 million odour abatement contract to Regina-based Gabriel Construction.
Foul-smelling gases emanating from the waste will be piped into bioreactors as a result of the upcoming work.
"We already have bio-reactors, where microbes destroy or eat up organic matter, so we’re just taking the foul air, the gases that stink, and putting it through there. That way we’re going to reduce the odour," said Larry Schultz, manager of engineering services with Saskatoon Water.
He expects a reduction in odours of close to 75 per cent.
The initiative is expected to be complete by January 2017, according to Trevor Sebastian, project manager with Gabriel Construction, which has a shop in Saskatoon, as well as several superintendents based in the city.
Preliminary work began on April 20, Sebastian said.
There will be a peak number of about 40 workers on site, but an average of 25 to 30, he added.
Other waste water treatment projects that Gabriel Construction has been involved in include one in Tobin Lake, another for the One Arrow First Nation, as well as a building and a reservoir for a sewage pumping station for the Town of Martensville, near Saskatoon.
The company also undertakes commercial, institutional, civil and heritage projects.
"Because we’re general contractors, we rely on our sub-trades for most of it. That’s why you’ll see the wide range (of projects)," said Sebastian.
The most challenging aspect of the odour abatement project in Saskatoon will be ensuring the new system functions as designed, he said.
"We just build them. Stantec designs them," Sebastian said.
"There’s lots of factors in between, but it is a fairly straightforward job, don’t get me wrong.
"They’re definitely confident of putting (the foul-smelling gas) in the bottom of the bioreactors, which are already existing. By the time it penetrates through all of this liquid, the micro-organisms will eat up the smell."
An odour study determined that by changing the fermenters to a different process, and by ceasing the practice of putting fermented sludge into the primaries (the clarifiers), then odours can be vastly reduced, Schultz said.
"In a nutshell, that’s what the project is. We’re going to stop the practice, we’re going to change the fermenter type, we’re going to put covers over these fermenters. We also have an open tank, we’ve covered that," he explained.
"We’re going to pull the smelly air off of these tanks and put them through the bioreactors and therefore reduce odours, by about three-quarters of the odours that are present in the plant."
Currently, solids undergo a fermentation process.
Some of that material is then placed in the primary clarifiers.
"Which is the first stage – sewage comes through and there’s these screens at the headworks, where they take out rocks and grit and things like that. And then, it goes into these basins," Schultz said.
"The first thing it does is (go into) primary clarifiers, where solids settle out. We also add some of this fermented sludge in there, and that’s what makes it stink."
There has not been any treatment of the air emerging from the waste treatment plant for years, and some residents have complained, Schultz acknowledged, although he said it hasn’t been a substantial number.
The wastewater treatment plant – constructed in the 1970s and located on Whiteswan Drive in the northern portion of the city and near the South Saskatchewan River – underwent a major upgrade in 1996 to convert it into a biological nutrient removal plant.
Along with its related lift stations, it employs about 50 to 60 people, Schultz said.
The plant – the only one serving Saskatoon – is designed to process up to 120-million litres of waste water per day.
The volume is generally about 90-million litres daily and its capacity is only put to the test during heavy rain, when it can temporarily accommodate up to 300-million litres, Schultz noted. The plant will remain fully functional during the odour abatement project, he added.
"There’s a considerable scheduling component to all of this which keeps the plant active while the work is being done," he said.
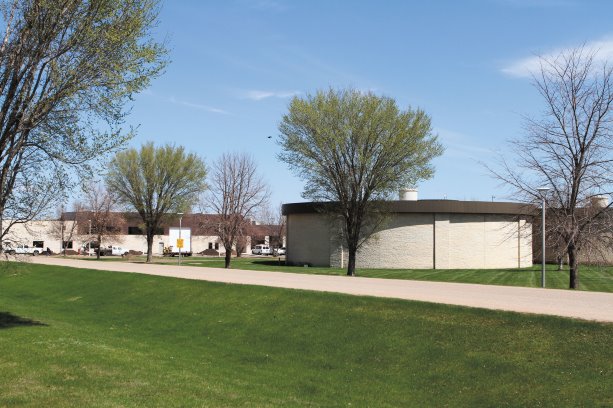
1/2
Saskatoon’s wastewater treatment plant is designed to process up to 120-million litres of wastewater per day. The plant is getting a new odour abatement system.
Photo: Derek Neary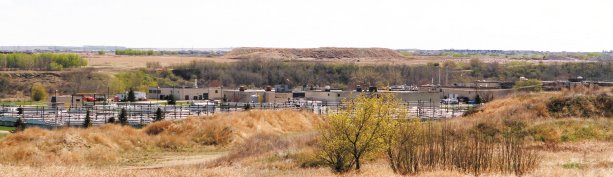
Recent Comments
comments for this post are closed