A 40-foot-long cross-laminated timber panel was unheard of in the mass timber world until EllisDon proved such a column-free system could be done — with a little help from post-tensioned concrete.
In collaboration with architectural firm DIALOG, the constructor has prefabricated a CLT hybrid timber floor system which consists of two “trenched out” channels inlaid with post-tensioned concrete.
It is a breakthrough that could see mass timber used in ever-taller commercial buildings.
The prototype is “a very strong, very slender long panel” that allows for exposed wood ceilings, Mark Gaglione, director of building and material sciences with EllisDon, told a packed seminar recently at the Mass Timber Seminar Conference at George Brown College’s waterfront campus in downtown Toronto.
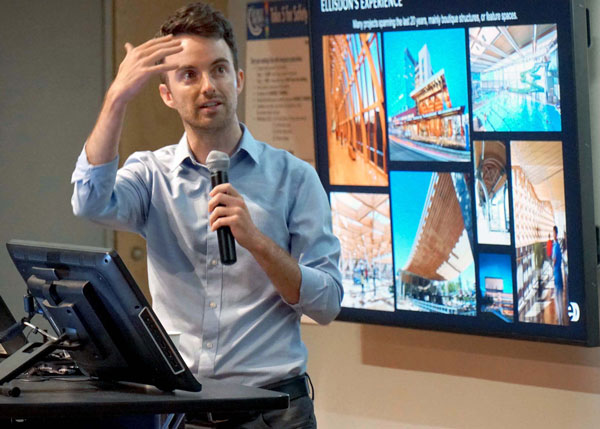
“This is one of the first times at EllisDon that we’ve taken a concept — a white paper and a bunch of renderings — and pushed it through a lot of friction to make it a real thing.”
While the hybrid span could be suitable for skyscrapers, it still requires extensive testing, Gaglione said.
The prototype panel has been tabulated at $17 a square foot more than conventional steel/concrete floors. About half of the premium was due to insurance costs, he said.
But that cost difference could narrow because the hybrid system is about a foot thinner than steel/concrete floor systems. That difference could translate to savings in multi-storey buildings through the elimination of materials for envelopes and elevator cores, Gaglione told the seminar audience.
For ease of installation, the premade panels would install like standard CLT panels, with a concrete monolithic topping poured over top that doesn’t require reshoring underneath. That would eliminate “a big drain on resources onsite,” he said.
It is not ready for market, however, he said, pointing out structural testing to date shows “serious optimization” is required to improve the prototype.
“Right now there is a lot of steel (rebar) in the panel’s channels. Iteration two will have 30 per cent less steel and we’re going to change the thickness of the panels.”
Testing to be done includes placing the panel in “a loaded position” for about 18 months at a lab operated by FPInnovations in Vancouver.
“We know how strong CLT and post-tensioned concrete is but what’s not well understood is the long-term response of hybrid structures.”
EllisDon will subcontract to itself to install the panels on the first projects.
“We want to control the manufacturing in the first go-around and come to understand this product better,” he said.
While the builder has fabricated the panels in-house in Ontario, it hasn’t decided if it will shop around for manufacturers when the hybrid system goes into full production. Eventually it might license out the technology, possibly to global companies.
Craig Applegath, partner at DIALOG, said the hybrid floor panel could be used in highrise buildings.
Typically, floor systems represent 70 per cent of the building materials that make up tall structures.
In DIALOG’s conceptual 100-storey hybrid wood highrise, EllisDon’s 40-foot hybrid wood flooring system takes centre stage, tied into the concrete core and steel exoskeleton of the building.
“It allows for a completely open (column-free) space and you get to see the CLT, which is what all the realtors and developers were telling us they wanted to see (in a commercial building),” he told a seminar audience at the conference.
The use of mass timber can be a green leap for the building industry, he added.
“Embodied carbon (emissions) from using mass timber…is between 13 to 25 per cent less than steel and concrete.”
The mass timber conference was organized by George Brown College, the Brookfield Sustainability Institute and Rothoblaas, an international company known for its connectors and other solutions for timber systems.
Recent Comments
comments for this post are closed