In east central Alberta’s Paintearth County, about 125 kilometres east of Red Deer, the Halkirk 2 (H2) Wind project is taking shape.
Twenty-eight towers, to be erected over 17,000 acres, are estimated to provide enough energy for roughly 57,000 homes, once operational
The developer is Edmonton-headquartered Capital Power and Quebec-based Borea Construction is the prime contractor.
H2 is being built as a follow-up to the nearby H1, where 83 turbines on 80-metre-high towers, have been turning since 2012.
Together, H1 and H2 are among Alberta’s largest wind projects.
Allowed to proceed in December 2021, H2 was first proposed to have 74 turbines. It was later was cut to 31 due to complaints from area landowners. In June it was further downsized by three more due to aviation safety and concerns from those living nearby.
Originally pegged to cost $274 million, the final figure will be higher, according to Capital Power’s senior adviser Michael Sheehan.
The number of workers at the site varies, depending on activity, but peak employment was around 300 people. In mid-July, roughly 215 workers were onsite, says senior project manager James Osness.
Towering turbines rise
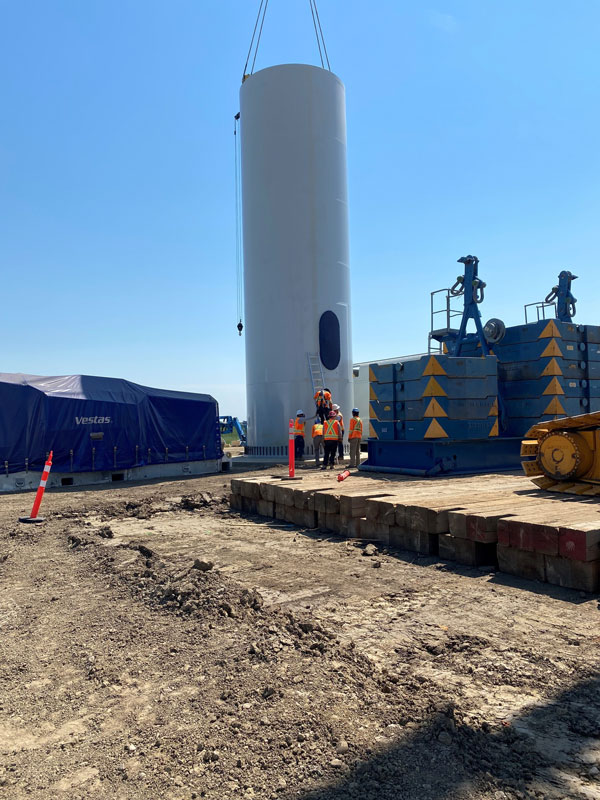
In early July, the first wind turbine components arrived for the 28 towers.
The components were manufactured in China, India and Vietnam and were shipped to either Vancouver, Washington State or Houston, Texas, Osness says. Turbines are the Vesta V150-4.5.
The tower sections, nacelles, blades and hubs are then transported, via truck, from a rail siding in Oyen, 210 kilometres away. Deliveries are anticipated to be completed before the end of August.
“We try to receive one complete turbine per day,” Osness says.
One turbine may require up to nine hauls: one nacelle, one hub, three blades and four tower sections.
Stages of foundation installation are excavation, mud-mat installation, base rebar installation, anchor bolt cage installation, rebar cage installation, base concrete pour, pedestal concrete pour and backfilling.
Each foundation requires 59 to 65 continuous concrete pours and can take up to 11 hours.
A fleet of 13 concrete trucks travel to and fro from Borea’s staging site, where a local batch plant has been built, Osness says.
The first base tower section was set in place at T9 on July 10 and wind turbine assembly for the project is expected to finish before the end of October. The final foundation pour was completed on July 7.
Grouting integral to alignment
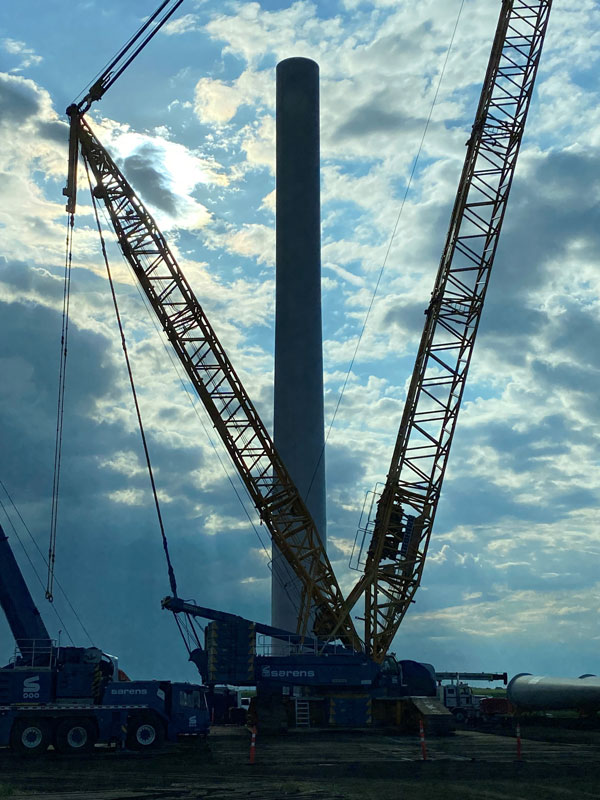
One important step is grouting, along the tower base, says Osness.
Grouting deals with load distribution, structural stability, alignment and levelling, protection against corrosion, vibration dampening and foundation integrity.
Weather conditions influence the work schedule.
For the grout to set properly, temperatures cannot exceed 30C for the first eight hours of cure time.
If daytime temperatures exceed 30C, Borea will do grout pours during cooler hours, beginning at approximately 4 a.m. or earlier.
The pours take roughly two hours and are forecast to be done by the end of August.
Weather also plays a role in the wind turbines’ operation. There is no upper temperature limit that would stop rotation, but when the temperature hits -32C, the turbines top, Osness says.
They can also withstand tornado conditions and have been built to seismic-level standards.
To assemble the tower, the three large blades on each tower are bolted to the hub; each rotor rotates at 14.5 RPM and is connected by a drive shaft to a gearbox that converts the revolution speed for the generator.
The three-phase generator inside the nacelle produces electricity, which is then converted by a transformer.
Once operational, the turbines will relay their power, via underground roadside connector lines, to substations and then to the provincial grid.
The best wind speed for power production is 60 km/hour; minimum wind speed is 11 km/hour and once winds are over 90 km/hour, a sensor located on the top of each nacelle will signal the main computer to shut down as a safety measure.
While 17,000 acres of farmland have been leased for the project, Sheehan says the project footprint is much less. Each tower takes up a 65-metre-by-65-metre gravelled area.
‘Social costs are high’
Landowners can continue to plant crops or graze livestock up to the gravelled edges, he says.
Nearby landowners have voiced concerns about H2.
Dwayne Felzien’s family has farmed in the area for 120 years and his family now owns 4,000 acres near the installation, where they raise livestock and grow crops.
While acknowledging the revenue being generated for the county by the wind projects is good, he says work on H2 has been disruptive.
Night construction has resulted in lack of sleep. The dust raised by the project has been excessive.
A lot of project-generated trash has been blowing into areas like coulees.
Wildlife has been impacted, since the towers are impeding migration routes, feeding and nesting areas and causing bird strikes, Felzien says.
“The social costs are high,” he says.
Landowners concerns have been heard, Osness says.
Traffic speeds are a maximum of 50 km/h. Calcium and water are being used to counteract dust.
An aircraft detection lighting system is being installed to mitigate the impact of required turbine lighting.
The biggest challenge has been the concrete pours because of heat limits. So some foundation pours were done during the night, Osness says.
Work is typically carried out from 7 a.m. to 5:30 p.m., five or six days per weeks, with occasional Sunday hours.
Osness expects H2 to be commissioned in December 2024.
Recent Comments
comments for this post are closed