SYNC111, an apartment building that lies just west of downtown Edmonton, was recognized recently by the Canadian Precast/Prestressed Concrete Institute (CPCI) as its project of the month.
CPCI’s project of the month highlights Canadian projects that promote the use of precast concrete.
Gardner Architecture in Edmonton acted as architect and prime consultant.
Company principal Ben Gardner says SYNC111 is a precast concrete structure with some steel load-bearing elements.
“We used precast concrete on the load-bearing exterior walls and hollow-core precast concrete on the floors,” says Gardner. “It enabled us to maximize site density. We were able to build up to seven storeys and, at the same time, keep the height of the structure to no more than 18 metres above grade. That meant it wasn’t considered a highrise structure, which saved a large amount on life safety.”
Gardner says there were several benefits of using precast concrete on the project.
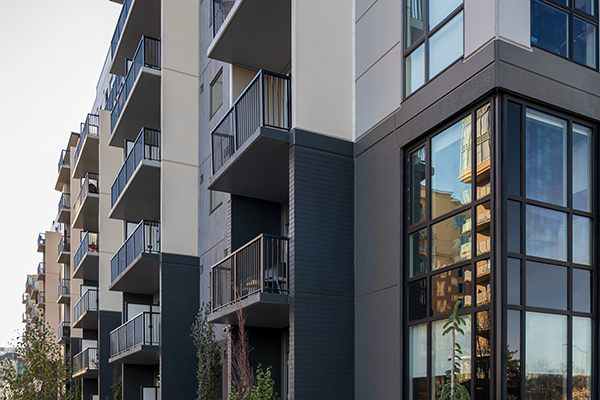
“The main benefits are cost-control and speed,” says Gardner. “Erection time was very quick, just a few months. We were shocked at just how fast it was.”
Other benefits were lower insurance costs during and after construction, better sound control and reduced vibration.
SYNC111 has a U-shape and fronts on a main avenue and the multi-use path in nearby Railtown Park on 110th Street NW.
The apartments on the main floor along the front facade are elevated above grade as much as possible to give residents privacy from the street. In addition, each suite has a private entrance to the sidewalk.
Parking is located inside the building, in the hollow part of the ‘U’ at grade level behind the main façade.
The parking facility is topped with a roof deck that is used by the tenants.
“Precast concrete was used on the entire parkade structure – columns, beams and walls,” says Gardner.
To reduce the cost of construction, SYNC111 was designed so that it is symmetrical north to south.
“The reason for the building’s symmetrical shape is that it reduces the amount of custom detailing that is required as well as the amount of time spent on co-ordination and data management,” says Gardner.
The weight of the building is supported on screw piles, with precast concrete panels in the basement acting as grade beams.
Most of the ceilings inside are unfinished and the underside of the hollow core floor slabs are exposed to given them an industrial loft look.
The exterior precast concrete walls are insulated double wythe (brick), with the windows installed in the wall panels in the precast concrete plant.
The outside faces of the exterior walls were also painted in the plant, with a final coat of paint applied to the finished building.
The inside faces of the exterior walls are concrete, with a painted gypsum-based skim coat giving them a smooth finish.
Window and door openings were sized to allow the exterior load-bearing walls to accommodate the vertical loads.
Brick form liner was used on balcony supports, and brick veneer, including bricks from the buildings that formerly occupied the SYNC111 site, was used at the south-east corner of the building, in the lobby and next to the main entrance.
Gardner says the balcony supports were exaggerated to help animate the building and to provide privacy to the apartment tenants.
CPCI is a technical institute that was founded in 1961 as a not-for-profit organization to educating designers producers, and owners of precast concrete systems.
Its purpose is to advance the structural, architectural and specialty precast concrete industry.
Recent Comments
comments for this post are closed