Ontario’s Ministry of Transportation is steadily increasing the number of prefabricated bridges it tenders each year.
Building Better Bridges
Speedier build ups prefab use
Ontario’s Ministry of Transportation is steadily increasing the number of prefabricated bridges it tenders each year.
“In the past two or three years, we’ve done some prefabricated bridges. Our aim is to go more and more into prefab. We are in the initial stages,” said Dr. Bala Tharmabala, manager of the MTO’s bridge office in St. Catharines.
The move by the MTO into prefabricated bridges began about five years ago when the ministry created an internal team to study the advantages of prefabrication.
Tharmabala said the advantages of prefabricated bridges are speedier construction and reduced traffic disruption, improved work-zone safety, reduced environmental impacts, improved quality, and reduced life-cycle costs.
“As we start, the cost can be slightly higher than conventional construction, but with time, the costs should come down,” said Tharmabala, at a seminar on prefabricated bridges, held at the 2006 Ontario Road Builders’ Association convention.
“In general, we want to do a quicker construction and at the same time keep costs similar, or as low as possible. The ministry’s vision is to develop and promote prefabrication technology and do what we can to achieve that end.”
The MTO’s first prefabricated tender was the Moose Creek Bridge, built in 2004 by Miller Paving Ltd. on Highway 101, south of Timmins.
In 2005, there were at least three MTO bridges completed using prefabricated systems. They are the Little Savanne River bridge, northwest region; Passé-a-Fontaine bridge, northeast region; and Sucker Creek bridge, eastern region.
This year, the MTO plans at least five tenders utilizing prefabricated bridge construction. One of those tenders involves erecting eight overpasses on Highway 417 in Ottawa.
“Those are basically heavy lift and move (projects). Where you build the bridge on the side and lift it and put it place,” Tharmabala said.
With conventional bridges, the concrete girders spanning the piers are put up, the forming is built in between them and the concrete deck is poured on top.
Prefabricated bridges speed up construction because the deck and girders are precast as one piece, said John Fowler, president of the Canadian Precast Prestressed Concrete Institute.
“They (the sections) just fit together and you don’t need to stop and form and pour a deck between or over the girders as is currently done,” Fowler said.
For the Moose Creek bridge, it took Miller Paving about a week to erect the precast abutments.
“Certainly the abutments would take a lot longer with a conventionally designed bridge,” said Ed Kalnins, vice-president of northern operations for Miller Paving. “This proves there can be timing efficiencies. But this one cost more than a conventional bridge because it was the first.”
The Moose Creek bridge did present some challenges for Miller Paving.
There were difficulties with the interlocking mechanism for joining pieces of the precast deck-and-beam sections, which Kalnins said was tough to fit.
“There’s a little gap that was supposed to be closed with a circular piece of neoprene. Where the neoprene goes, that’s the part that doesn’t fit very well,” he said. “So we have got to come up with a different way of doing that, but still getting the seal.”
Another problem was with allowable tolerances for a two-foot-wide section of cast-in-place concrete on the deck. Known as a closure strip, this cast-in-place concrete seals together the sections of precast deck.
A local inspector required Miller Paving to grind areas on the edges of the precast sections to achieve a level of exactness for the bridge surface that Kalnins feels was extreme.
“The inspector was trying to make it too finicky, too exact. It’s not necessary to do that,” Kalnins said.
The finish on the bridge surface would look the same, “if we had done none of that grinding and everything,” Kalnins said.
Would Miller Paving take on another prefabricated bridge?
“We would,” said Kalnins. “But we’re a lot smarter now.”
Tharmabala said next on the MTO’s agenda for prefabricated bridges is increasing standardization of bridge elements to further reduce construction times and traffic disruptions.
“There will be issues, but I think we can move a little more towards standardization. And that will automatically reduce the cost, too,” Tharmabala said.
Fowler said because the girder and deck sections for the Moose Creek bridge were non-standard sections, the precast contractor, Pre-Con Ltd., had to make customized wooden forms.
“Until they tried a couple, they didn’t want to make the commitment to buy steel forms,” he said.
“Once the sections have been established and agreed upon, between the MTO and the industry and the consultants, then the pre-cast industry will purchase steel forms and this will become the standard way of doing things.”
The precast industry is certainly happy with the MTO’s move to more prefabricated bridges, Fowler said.
“And probably the most significant way to speed up construction is do more of it in a factory and less of it on the job site, which is right up our alley,” he said.
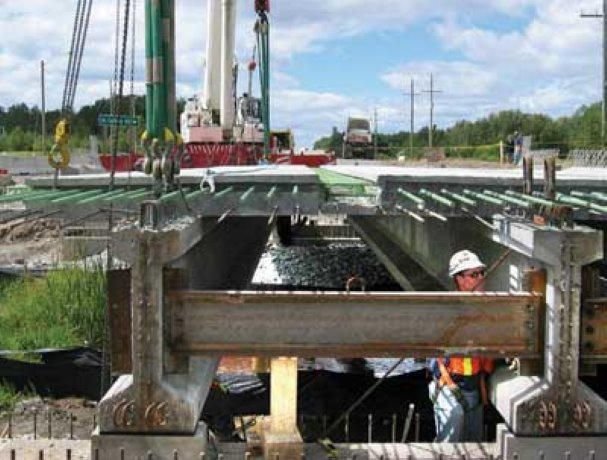
Recent Comments
comments for this post are closed