As part of the federal government policy to enforce sovereignty in Canadian waters a massive redevelopment of Irving Shipbuilding’s Halifax Shipyard is underway and that, in turn, is generating a lot of work and a fair number of challenges for an Ontario firm.
Hamilton, Ont.-based Walters Inc. is the supplier, fabricator and erector of approximately 9,000 tons of structural steel for a new 1,200-foot-long, 200-foot-wide, three-section production plant consisting of 45, 200-foot-long, 16-feet-wide, 22-ton trusses.
To be used for building Arctic/Offshore Patrol Ships (AOPS) for the Canadian Navy, the plant will include a 125-foot fabrication high bay with a 200 metric tonne capacity, and a clear span of 180 feet across from crane rail to crane rail.
Hatch Mott MacDonald (HMM) is the prime engineering consultant for the overall redevelopment of the approximately 20-acre shipyard, as well as being the architect and structural engineer of the building. Ellis-Don is the construction manager.
Nine thousand tons of steel including the trusses and a metal deck are being supplied by Walters, says Mark Koppelaar, the company’s vice president of projects.
“We got the job in July,” says Koppelaar, adding that preparing for the project has required a lot of planning.
But shop drawings were underway in August and by September, fabrication of the steel was underway. Components such as columns, platforms, crane girders, and purlins are being fabricated in Walters three Ontario plants; Princeton, Stoney Creek and Hamilton. Approximately 90 per cent of the Princeton plant’s production facilities and 50 per cent at the Stoney Creek are dedicated to the project.
Fabrication of the trusses was subcontracted to Cherubini Metal Works in nearby Dartmouth, N.S.
“They are fabricated in three sections, assembled on-site and lifted as a single piece,” says Koppelaar, pointing out they have to be aligned to very tight tolerances over more than 5,000 square feet of crane rail.
By shipping the steel at night, by truck, the company is able to deliver the material on time, avoiding potential delays such as traffic congestion and not being able to book trucking space, says Koppelaar.
Erection of the steel started in February and within a record two months, 2,000 tons had been lifted into place.
“We’re averaging about 250 tons a week,” adds Koppelaar.
A five-person supervisory crew from Hamilton is overseeing the work which is being carried out by locally hired workers. Some of the equipment being used includes a 230-ton crane and a number of 200-ton crawlers.
“We have three raising gangs working on different areas to expedite the very tight schedule. It (the multiple teams) requires a lot of coordination.”
A peak workforce ranging from 45 to 50 employees will be on-ite, although that will vary, he says.
The new plant will replace an older one which was being demolished just as Walters was coming on-site. In addition, there is other construction underway. As a result, access to some areas of the shipyards is restricted. But the footprint of the new plant is clear for laying down equipment, he says.
One of the hazards of the job, especially at the higher heights of the building, is the fog drifting in from the harbour.
“But we’ve maintained an excellent safety record and we’re still on schedule,” says Koppelaar, who expects that Walters will be finished and off the site by this coming December.
While completion of the building will not be until early 2016, construction of the first ship is scheduled to commence in the second half of 2015, says Hatch lead structural engineer Robert MacCrimmon
Some of the other construction underway, as part of the redevelopment, includes two new wharves, a ship erection platform at the wharves, a new parking garage and a new plate shop across in Dartmouth, says MacCrimmon.
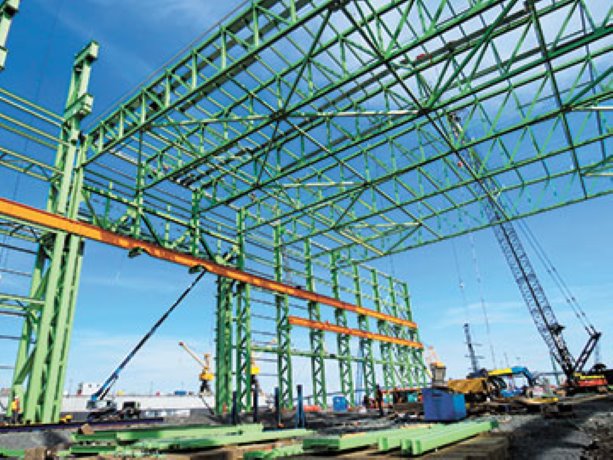
Recent Comments
comments for this post are closed