More than a century ago workers at the sprawling Gooderham and Worts distillery in Toronto’s east-end would store whiskey barrels in two large masonry rack houses.
That distillery has been transformed in the Distillery Historic District and, if those workers could come back to life, they might be tempted to drink a toast in recognition of an intricate three-phase restoration and reconstruction of the rack houses.
Constructed in the late 1880s, the 10,000-square-foot buildings are being given a new life as part of a retail/residential venture by the Distillery Development Corp., the developer of the Distillery District which contains more than 40 brick and stone heritage buildings.
Designed by E.R.A. Architects and carried out by Historic Restoration Inc., the soon-to-be completed restoration encompassed the retention, repair, and stabilization of a wall on one of the rack houses, two on the second, and the careful dismantling and reconstruction of the other five walls, followed by the equally painstaking task of reconstructing those walls.
The phased restoration was necessary to facilitate the construction of a 50-foot-deep, four-level, underground parking garage which will serve two high rise condominiums being built by the developer (architectsAlliance is the designer of the condominiums which were built by Tucker Hi-Rise.)
Surrounding the podium of one of the condominiums — as well as being underneath and inside, the rebuilt/restored walls will be the face of a number of ground floor retail shops and boutiques, says E.R.A. principal Andrew Pruss.
The 37-storey-high condominium is built above the rack houses with an amenity area including a swimming pool, he says.
Many of the original doors have reinstated in the shops — although other openings were required and, what had been a laneway separating the two structures, will be a main corridor, says Pruss.
“We had to understand how this would proceed,” says Pruss, in an overview of the different elements of the sequenced restoration. Design work first started in 2006.
For Historic Restoration the project required its first site visit in 2010. The three walls selected to remain in place were restored, with new underpinnings installed and then braced. Other work included the installation of a copper Damp Proof Course in sections between the rubble stone foundations and the brick masonry to prevent moisture from rising up through the bricks, says partner Paul Goldsmith.
As well, the backs of each stone on the foundations were cut to create a four-inch thick veneer, which was later re-laid around the base of the reconstructed walls, he says.
The walls had to “be solid enough to remain place” during the dismantling of the other walls, which was the next priority.
“Each brick had to be treated like an antique,” says Goldsmith, explaining this was a restoration, not a demolition.
“One of the challenges of this project was to carefully dismantle, clean and stack the bricks without causing damage to the edges or faces of the bricks. Exterior wythe bricks had to be carefully separated from the middle and interior wythe bricks so that they were used in the correct position during the rebuild.”
During that initial repair phase, face bricks were harvested from the areas to be dismantled and were used to repair the facades that were retained in place, he points out.
In all, approximately 160,000 bricks were removed. As well, the huge interior timber racking system was salvaged and trucked away, he says. (A significant component of the lumber was reused in the building of the condos.)
Reconstruction of the walls commenced in 2012 after the underground parking garage was completed. A number of Dorset Multi Red bricks imported from the United Kingdom had to be installed because many of the original were used in the repair phase or weren’t suitable for re-installation.
“They’re (the new bricks) similar in size, colour, and composition.”
The exterior walls are comprised of three wythes (or sections) structurally attached to the interior poured and concrete block walls which, in turn, have been covered with a layer of bricks.
One of the construction hallmarks of the rack houses was the lack of expansion joints. That’s because they were built with hydraulic lime and that’s exactly the same system Historic Restoration has used in their rebirth.
Hydraulic lime creates a breathable, flexible mortar, very similar to the mortar used for the initial construction. It allows the walls to breathe and shed water through the masonry joints thus protecting the bricks from becoming saturated and deteriorating under freeze/thaw conditions, says Goldsmith.
“There is not one bit of cement in these walls.”
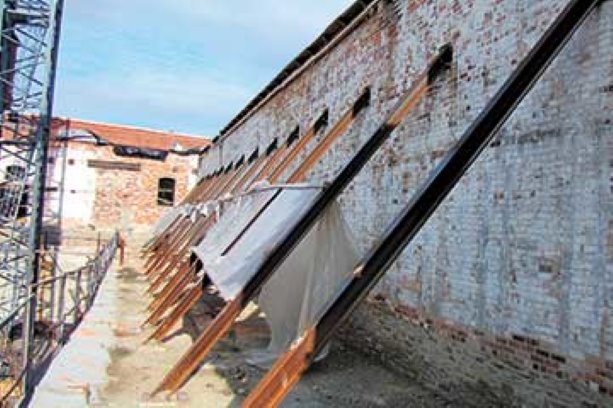
Recent Comments
comments for this post are closed