Well known for its masonry restoration work in and around Toronto, Limen Group traveled east to Saint John to complete the retrofit/restoration of an historic granite and sandstone-clad commercial block in the heart of that New Brunswick city.
Limen was the general contractor for the four- and five-storey complex featuring Postal Station A, a Beaux Arts style building erected 1913-15.
The contract also called for the restoration/reconstruction of a brick and masonry addition built in 1952 behind the old post office. Both buildings are owned by Public Works and Government Services Canada (PWGSC).
The contractor’s responsibilities included masonry work such as stone graft repairs — commonly called Dutchman repairs — stone resetting, composite stone patching, stone rubbing and fracture repairs using stainless steel rods, explains Arran Brannigan, vice-president of operations of Limen Group.
“The contract focused on conservation and restoration, rather than replacement (of old with new elements).”
Some of that work has been tricky. Take the damaged second floor sandstone columns/capitals flanking the windows, for example. Getting the rough finish right on Dutchman repairs to the curved portions of the columns was one thing; achieving a perfect final finish was another, Brannigan says.
The work didn’t get any easier for the florets on the column capitals, he adds. “Splicing a piece of cut stone to match the floral design was a precise task requiring highly skilled individuals to create a seamless repair.” Only a handful of masons have the skill to perform the work.
Repairing decorative column capitals also was a challenge because some sections had to be completely replaced. The work started with stone carvers creating rough carvings from templates of the originals offsite and then installing them on the building and “touching them up” to fit, says Brannigan.
Another challenge was how to perform structural repairs to the building’s steel frame without damaging the masonry façade. Limen Group collaborated with project architect DFS Inc. to devise a concept for a shoring system to support the wall, minimizing façade intrusion during steel frame repairs.
“Originally, we were expected to remove 60 large pieces of stone (including cornice stones with dentil features) from the façade to get to the damaged steel but with the shoring system we came up with we only had to remove four stones,” says Brannigan.
The steel frame was damaged by years of water penetration into the building through an interior rain gutter system. Repairs included welding new steel plates to the existing steel-frame structure. Masonry walls were stabilized using Blok-Lok stainless-steel helical ties. New copper flashing and copper drain lines were installed.
While the general contractor did all the masonry work itself, it subcontracted the work to repair the original wood windows. The job involved “scarfing” new wood to match the existing and grafting larger wood pieces to sections with extensive damage and rot. The masonry façade of the annex required extensive repointing. A Type N mortar (with some lime content) was used. The building also required some brick replacement and concrete window trim repairs which were protected with a “breathable” cementitious waterproof coating.
Brannigan says because the two buildings were constructed to the lot edge on busy downtown streets, the building team had little room to work on outside. There was no space at grade at the annex for a heating plant to protect masonry work in winter so the plant was set up on the roof, hoisted there with 110-tonne crane. Scaffold and tarping covered all sides of the project for most of the 18-month construction period. Night shift and weekend work was mandated to accommodate daily activities in the area.
Brannigan says for the project’s duration, the building had to remain fully operational so it was critical to minimize disruptions. Some tenants had to be relocated during interior repairs to the structural steel and drains. Meeting that objective was made easier with the cooperation of PWGSC “and the extremely understanding building tenants.”
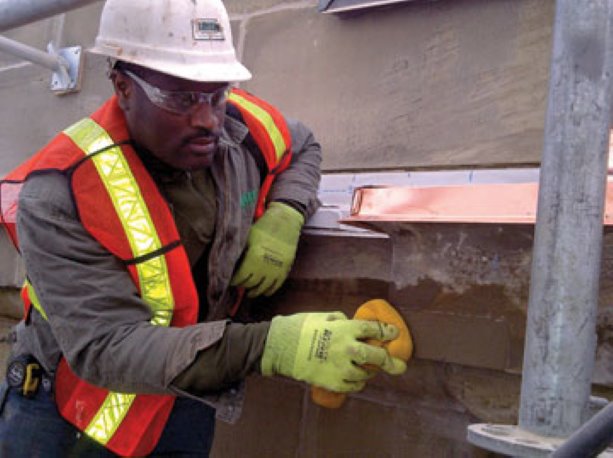
1/2
Photo: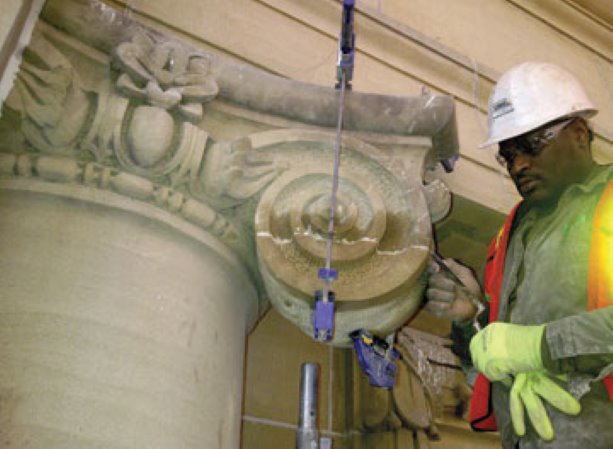
Recent Comments
comments for this post are closed