It’s inevitable: Build a road and sooner or later it’ll crack.
Filling those cracks is a priority maintenance job because left unchecked the pavement is exposed to water and debris which will work their way into the substructure and cause further and much more substantial damage. More to the point, sealing cracks quickly is a cheap fix which can save hundreds of thousands in replacement costs.
The most common method of crack sealing is to rout and seal with hot-poured rubberized asphalt and it’s something done every day across Ontario highways. The trick, though, is which sealant for which application and if you filled a room with 100 road engineers from 100 different jurisdictions you’d likely get a couple of dozen different specifications.
“Currently, conventional standards like ASTM D5329 are used to select hot-poured crack sealants in Canada and across North America,” said Imran Bashir, bituminous engineer, materials engineering and research office at MTO. “These were based on empirical material properties such as penetration, flow, softening point, resilience and bond test, but do not measure a sealant’s fundamental rheological (deformation and flow) properties.
“The specification limits for these tests vary from one highway agency to another, so sealant manufacturers and suppliers must meet different specification limits for the same test and climatic conditions. This creates difficulties because many agencies with the same environmental conditions specify different limits for the measured properties.”
To better seal the deal on crack solutions, the Ontario Ministry of Transportation (MTO) has partnered with U.S. state agencies, manufacturers and academia in a transportation pooled fund study sponsored by the Federal Highway Administration (FHA) which is testing and monitoring a range of specs under differing environmental conditions.
It hopes to develop performance-based guidelines to better identify which sealant is best for which application and which location, given local weather patterns.
Ground Zero for the Ontario portion is a section of Highway 35 near Lindsay, Ont. The study is being led by the Virginia Department of Transportation and the Virginia Transportation Research Council, with researchers from the University of Illinois at Urbana-Champaign acting as validators. It is one of eight test sites in a variety of climatic regions across North America and under different traffic conditions over a three year program.
“We (MTO) have partnered with other U.S. state agencies through transportation pooled fund studies before,” Bashir said. “Participation in a pooled fund type study is a cost-effective way for the ministry to pursue research projects and new technologies.”
It was a natural progression, he said, since the MTO had been involved in Phase 1 of the pooled fund research project TPF-5(045), the development of performance–based guidelines for selection of bituminous-based hot-poured pavement crack sealant. This created an innovative sealant grade system for selecting hot-poured crack sealant based on environmental conditions, new performance-based tests and characterizing sealant guidelines for hot-poured sealant selection. This was led by the University of Illinois at Urbana-Champaign and the National Research Council Canada
“After completion of Phase I, MTO was approached by the Virginia Department of Transportation to take part in Phase II of the pooled fund study TPF-5(225), which is validation of hot-poured crack sealant performance-based guidelines which proposes to validate the (Phase 1)-developed performance-based guidelines.”
Highway 35 was chosen because it’s a secondary highway with one lane in each direction and gravel shoulders. The test section meets the criteria as a wet-freeze climate zone with good structural pavement strength, flexibility, and rideability, Bashir said.
“The trial section portion is about 8.9 km, with 16 trial sections in the northbound lane,” he said. “The contractor used a CIMLINE Magma 230 kettle equipped with a heated hose, wand and pump for the trial sections. They also used a rubber squeegee to provide an overband configuration.”
Bashir said stainless steel pins were installed on each side of selected transverse cracks at selected locations for future monitoring of horizontal crack movement. Wireless thermocouples were also installed in the pavement at selected locations for monitoring the pavement and air temperatures.
In addition to the routine rout and seal per MTO specs, several alternative methods have been applied, including variations of rout geometries, a clean and seal method without routing, a control section with no crack sealing, and different crack sealants. Seven crack sealant products, including a sealant typically used in Ontario, were placed in three rout configurations, including two clean and seal sections, Bashir said.
“Clean and seal (just crack filling without routing) is the easiest and simplest process whereas rout and seal is more complex,” he said. “Current MTO specifications allow the clean and seal process for cracks that are more than 15 mm in average width. The clean and seal process is not suitable for cracks experiencing active movement or narrow cracks.”
While the final report for the project won’t be out until 2014, so far, so good, Bashir said.
The Highway 35 trial sections were constructed in September 2011 and the first field evaluation was completed in March 2012, he said. “These trial sections will be monitored annually for three years but based on visual inspections carried after six months, all trial sections on Highway 35 are performing well.”
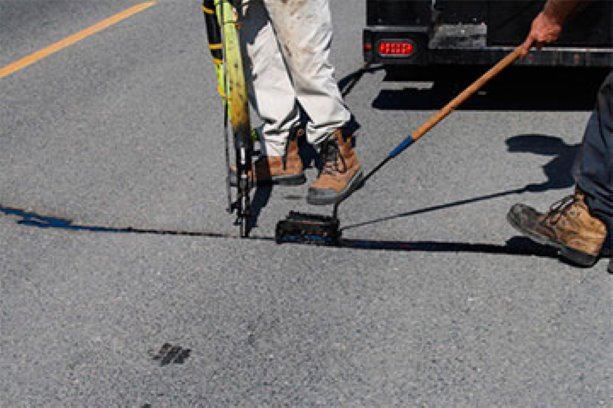
Recent Comments
comments for this post are closed