The Gordie Howe International Bridge’s concrete jump forms have a distinctly different look, fitting for a massive international project that will build the longest cable-stayed bridge in North America.
The jump forms, common on all bridge and tower work for concrete pours, are different in a couple of ways. That’s because the lower sections of the two bridge towers, on the Canadian and U.S. sides, have two rather than one pylons or “legs” rising at the same time. The fact the towers are in different countries also give the forms different looks.
On the Canadian side the box-like forms have a red motif, appropriate for Canada’s colours. In the U.S. the boxes have a blue look for America’s colours. Also, in Canada, the boxes, covered on the sides by sheet metal, depict Indigenous art, created by native artists in southwestern Ontario.
On the U.S. side the boxes sport American symbols such as an eagle and the “Spirit of Detroit,” the City of Detroit’s iconic symbol. The colours also match the tower cranes above, the Canadian crane painted red and the American crane blue.
Progress has been made in climbing the forms as they rise along the two legs of the inverted Y-shaped lower section, which totals 140 metres. The first pours took place in January this year and in late October the forms were at 45 per cent height of the tower’s overall planned 220 metres and well above the bridge’s road deck of 42 metres.
Once the lower sections are complete and come to a point, the single pylon head measuring 80 metres will top it. The pylon heads will house the bridge’s cable stayed system holding, which is 216 parallel strand stay cables.
Because of the lower tower section’s two pylons another innovation had to be developed.
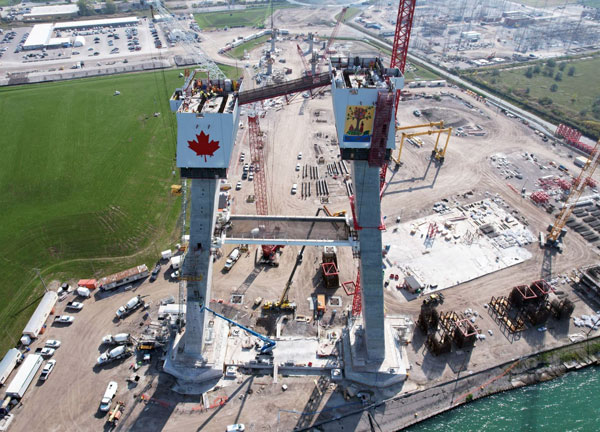
Exterior construction elevators take crews up to the forms. But because of expense and the fact the tower cranes hover above, the elevators could only be built along one leg.
Each elevator can hold six people and climbs 40 metres per minute.
But the 15 to 20 crew members working in each form obviously had to be able to get over to the other leg’s form. Hence a catwalk was constructed.
It’s a steel truss with decking and railings so crews can safely cross. Initially it was 36.4 metres in length and weighed nine metric tonnes. But as the forms climb the distance between the legs lessens.
If one form is temporarily jacked slightly higher before the other is raised the catwalk can still be used safely at a maximum 30-degree angle.
The form boxes themselves are five metres in height surrounded by sheet metal with two inches of Styrofoam for insulation. A form’s crew consists of ironworkers, general labourers and operators.
“At any given time, we always have to be worried about the load we put on there because it’s only good for a certain amount of weight,” says Terry Poole, the Gordie Howe bridge project director. “Not that 20 or 25 guys are going to break it, but we’ve got to maintain with the pounds per square feet we’ve got on there.”
Within the forms, concrete is pumped up to a mini placer via a slick line, in turn attached to a static pump on the ground. It’s filled by a continual schedule of concrete ready-mix trucks.
In the form, concrete is poured through the rebar, a total of approximately 130 cubic yards for a typical “lift” or segment. The forms then “climb” to the next level through a series of support brackets and screw jacks, powered by electric motors.
Poole says every project has its own “learning curve” and this one was no different. Staff had to figure out the time to complete the entire towers and the length of lift pours.
“So now that we’ve got the bugs worked out, we’re on a pretty good consistent six-to-eight-day cycle,” he says.
Completion of the entire towers — which will rival Detroit’s highest skyscraper, the GM Renaissance Center — should be reached in the fourth quarter of next year.
Poole says what’s relatively new on the project is use of a mini placer. Though used often on highrise building construction they haven’t been used much on bridge tower construction though one was used on Edinburgh’s Queensferry Crossing, completed in 2017, on which Poole also worked.
“They haven’t used that very much here in North America,” he says.
Now that tower work has surpassed the road deck level, crews are about to pour concrete for the corbels or brackets that will hold the road deck until the cable stays are attached. Crews will set up falsework, then forms, place rebar and pour concrete at the corbel locations.
Steel for the deck will start arriving later this year. That’s when the next aspect of bridge construction, noticeable to the eye, will take place.
“So, while we’re still going vertical, we’re going now to start building out horizontal,” says Poole.
Some general facts of tower construction: each tower will require 10,000 cubic metres of concrete and 4,500 metric tonnes of rebar. Once completed, the weight of each tower will be approximately 30,000 metric tonnes. Together, the bridge towers and cable system will be rated at 151,060 kilonewtons (kN) to support nearly 34 million pounds of weight.
Have there been project challenges?
“Huge challenges,” on what will be the fifth longest cable stayed bridge in the world, Poole says. COVID of course has been paramount, but the project has kept on schedule maintaining a late 2024 projected completion.
“The guys and the gals out there, they deserve all the credit because of working through this darn pandemic and being so diligent with our whole safety protocol,” he says.
We supplied concept sketches to BNA back in 2018 on the placing equipment needed to get concrete pumped to the top of the tower. The equipment we eventually supplied was completely different from the initial concept, but it’s incredible how the plan came together and it all worked out.