COVID-19 placed numerous challenges on the construction industry, including mandatory onsite testing, strict operational protocols and separating workers as much as possible.
For at least one Ontario ICI contractor it forced a complete pivot.
Faced with a precipitous drop in commercial construction projects at the height of the pandemic, what is now BECC Modular shifted from traditional onsite construction to a fully integrated design-build modular manufacturer and general contractor.
But the turnaround wasn’t instantaneous.
“We didn’t know what we were going to do (about the decline) at first,” says director of sales Peter Schoettle, who had just been hired in that role for what was then BECC Construction.
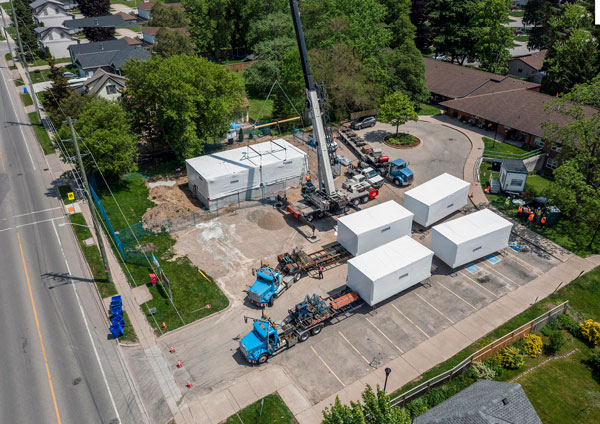
At the same time, Schoettle says he could see a need for medical buildings to address the pandemic and that modular-style ones would be a better alternative to the tents which were being used by medical and health care officials in the pandemic’s early days.
With the support and encouragement of CEO and company owner Ali Ozden, he began researching the market potential of modular construction and the technical hurdles that would have to be mastered.
For his part, Ozden, who had been contemplating a move to modular before the pandemic, also went on more than a few international fact-finding visits to countries with a high percentage of modular buildings.
With the help of an outside team of experts, the company began the transition to modular, specializing in the delivery and assembly of cold-formed steel, 12-storey maximum units.
That shift was not without a considerable number intense brainstorming and more than a few anxious moments, says Schoettle.
In 2021 BECC Modular leased a vacant 5,574-square-metre former stainless steel water purifying factory. Fully equipped with cranes and other equipment, which was utilized, the plant is located in Ancaster, a historic town in Hamilton, Ont.
Not only are Hamilton’s steel suppliers close by, the company has access to the region’s skilled steelworkers, which Schoettle describes, “as the best in the world.”
“We started off small,” says Schoettle, explaining the business strategy was to initially seek small scale projects so that the company would gain experience and knowledge before pursuing larger and more complex ones.
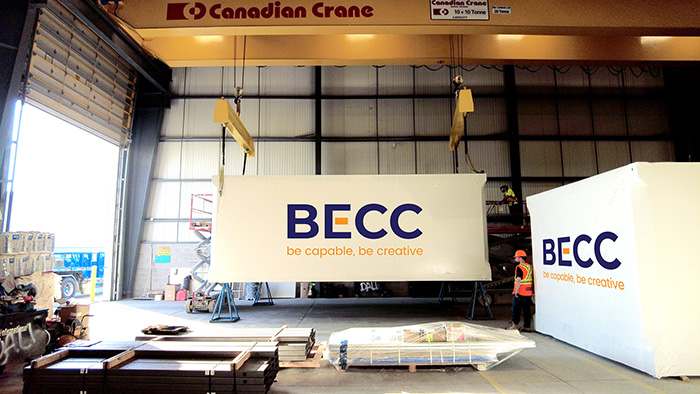
Since then, its business portfolio has expanded and BECC Modular recently acquired 2,787 square metres of leasable space in an adjacent building to meet market demand.
It’s currently producing units for a number of affordable housing projects in different parts of Ontario including a 32-unit building in Ottawa, a 24-unit one in Sarnia Ontario and a 27-unit building in Chatham-Kent.
Its skilled trade workforce has also steadily climbed and now stands at approximately 100. Included in that list are steelworkers, drywall installers, electricians, welders and tile layers.
That figure doesn’t include project managers, procurement personnel, support staff and in-house architects and engineers who produce shop drawings and work with outside architects.
“We’re a manufacturer,” says Schoettle, who prefers the term “assemble” rather than construct to describe the activity that occurs daily on its four production lines.
The first stage in the assembly process is erecting the outer frame, then inserting the infill light gauge steel, followed by the installation of the electrical wiring, plumbing, drywall, flooring and other components.
After a unit has been assembled, it’s shrink-wrapped and trucked either to a holding facility or directly to the building site. There is little material waste, the components are installed to very tight tolerances, and the units are CSA A277 certified, says Schoettle, citing some of the benefits of modular.
Another is employee comfort and safety. As the factory is heated in the winter and air conditioned in the summer, those workers aren’t battling the elements. They also have access to clean washrooms and a cafeteria.
BECC Modular is a turnkey service provider, including foundations and site work. But it does want to partner with general contractors which would allow it to concentrate on manufacturing and installation, says Schoettle.
Forging closer links with traditional contractors is a key objective of the Charlottesville, Va.-based Modular Building Institute, the international non-profit trade association serving the modular construction sector.
Modular is never going totally replace traditional onsite construction, says the institute’s executive director Tom Hardiman.
At the same, Hardiman, who has held that position since 2004, says he has “never been more excited about the growth of our industry.”
Modular construction now accounts for about six per cent of the North American construction volume. Driving that growth has been the need for medical buildings in the wake of the pandemic.
Other factors also at play include the skilled worker shortage and the need to address the housing shortage. In fact, the production of multi-housing units accounts for 30 per cent of total factory volume output in North America, he says.
While the six-per cent figure, “may not seem like much” that market share has doubled over the past five years and tripled over the past seven years, says Hardiman.
At the same time, North America lags a number of European countries, some of which offer incentives to spur modular construction, he says.
“But we’re getting there.”
Recent Comments