This spring, a 650-tonne mobile crane — one of the largest in Ontario — will hoist a pre-finished four-storey cupola and religious cross atop a steel frame to adorn St. Joseph’s Ukrainian Catholic Church in Oakville, Ont.
This spring, a 650-tonne mobile crane — one of the largest in Ontario — will hoist a pre-finished four-storey cupola and religious cross atop a steel frame to adorn St. Joseph’s Ukrainian Catholic Church in Oakville, Ont.
It’s a novel job for structural steel fabricator/erector M&G Steel Ltd. because the contractor is erecting the steel superstructure starting from the roof down to the foundations, rather than erecting it from the bottom working up.
“We’re doing it this way to allow for the installation of the exterior finishes, such as the slate roof, at lower heights,” says Chris Adach, project manager with M&G Steel.
“It creates a safer and simpler work environment for the trades, which otherwise would have to reach up to 80 feet on very steep roof lines.”
Working on a church is rare for a steel company like M&G. Working on one as unusual as St. Joseph’s is even rarer.
The 43,000-square-foot building contains 275 tonnes of structural steel and open web steel joists comprising the superstructure. When completed, the church will feature six 40-foot towers capped with steel-framed cupolas around a centerpiece 38-foot tall cupola towering almost eight storeys above grade.
Prior to raising the main cupola into place, it has been installed on temporary foundations and substantially finished, says Adach.
To fabricate the steel, M&G used CNC information downloaded from its 3D drafting model gleaned from the architectural and structural drawings.
To ensure accurate fit-up, a six-axis HD plasma robot called a Python cut each steel element.
The robot’s work also provided a steel framework with clean lines, explains Adach.
He says the steel frame has “unique weldments” which meet the architect’s specifications for a design that evokes architectural traditions of the Ukrainian culture and faith.
The steel contractor was retained by Santoro Construction, the job’s project manager, in the early stage of the preparation of working drawings to help develop the steel geometry and co-ordinate the overall design with the project’s architect, Wasylko Architect Inc.
“The architect teamed up with us at our office to visualize solutions from a 3D drawing model (SDS 2 software),” says Adach.
Such collaborations require a commitment on both sides to share knowledge and expertise of design and fabrication methods.
“In a way, it is a work in progress until the final touches are incorporated and the client is satisfied.”
To complete the shop drawings, M&G also worked closely with the structural engineer Strik Baldinelli & Associates to develop complex connections based on the factored loads and building code considerations.
Adach says M&G’s engineering team has had to come up with solutions on how to interface “difficult joint” connections. M&G worked with technicians to model the superstructure, draftspeople to detail steel components and checkers to ensure quality control.
Along with the complexity of the cupola, Adach says the steel company faced other challenges such as the fast-track schedule, fieldwork through the winter and limited access to the site, which borders busy streets and a residential area in Oakville.
“Once the crane was on site, it had to be perched on top of the first floor in the main entrance to allow a minimum radius for lifting the heavy cupola.”
The church’s entry will be completed once the cupola is in place this spring.
He says co-ordinating work with such trades as masonry and precast planks is critical to meeting the tight deadline.
Steel installation for the church is being done by K.C. Welding.
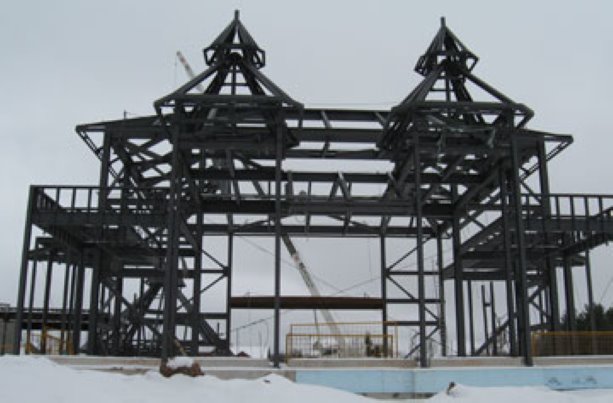
Recent Comments
comments for this post are closed