It’s one thing for architects and engineers to create flowing structures to enhance esthetics in public spaces, but the execution is often a massive challenge for the construction crews.
And that’s the case in point at the Toronto Transit Commission’s Pioneer Village station on the $3.2 billion Toronto-York Spadina subway line extension where three critical components triggered some deep thinking.
Clearly the execution by Limen Structures hit the mark set by the IBI Group designers, winning a 2018 Ontario Concrete Award in the Architectural Merit-Cast-in-Place category for the exposed architectural concrete which included a curved ceiling slab, iconic rock-wall and massive sloped elliptical columns.
Amir Soleimani, general manager of Limen’s formwork division, says when they first saw the plans and realized the scope of the formwork required there was a little bit of head scratching.
“ICI (Industrial-Commercial-Institutional) is always more challenging than residential, generally,” he says. “But this was a real challenge. Still, it was an honour for us to get the contract and do the work and, of course, win this award.”
The elliptical columns required a little trial and error to get the curves right and to ensure that the pieces would fit together seamlessly and still accommodate the required rebar, he says.
General contractor Walsh Canada was working with engineers WSP Canada on the $225 million station. St Marys CBM provided the mixes with Harris Rebar installing the metal work.
The elliptical columns rise from the platform level at different angles, there was no one-size-fits-all forming.
“These elliptical columns go from the raft slab to the saddle slab,” says Soleimani. “There are 19 of them, six are in two sequences and two flow from top to bottom. The highest is 12 metres; the lowest is some six metres.”
To pour them into forms meant sectioning the biggest columns into three pieces, Soleimani says.
“Four were in doubles, so eight columns and the rest were singles,” he says. “In some we used the same middle but custom-made forms for the top and bottom because they were different heights.”
The curves meant going to fibreglass forms, he says, and that mean some intricate engineering.
Limen brought in a consultant to design the forms using some high-level engineering 3D software. They sent the data to a specialty manufacturer in Texas.
Tying the rebar in was also tricky because it added pressure to the forms and had to be tied in at specific X-Y-Z co-ordinates before the fibreglass was installed.
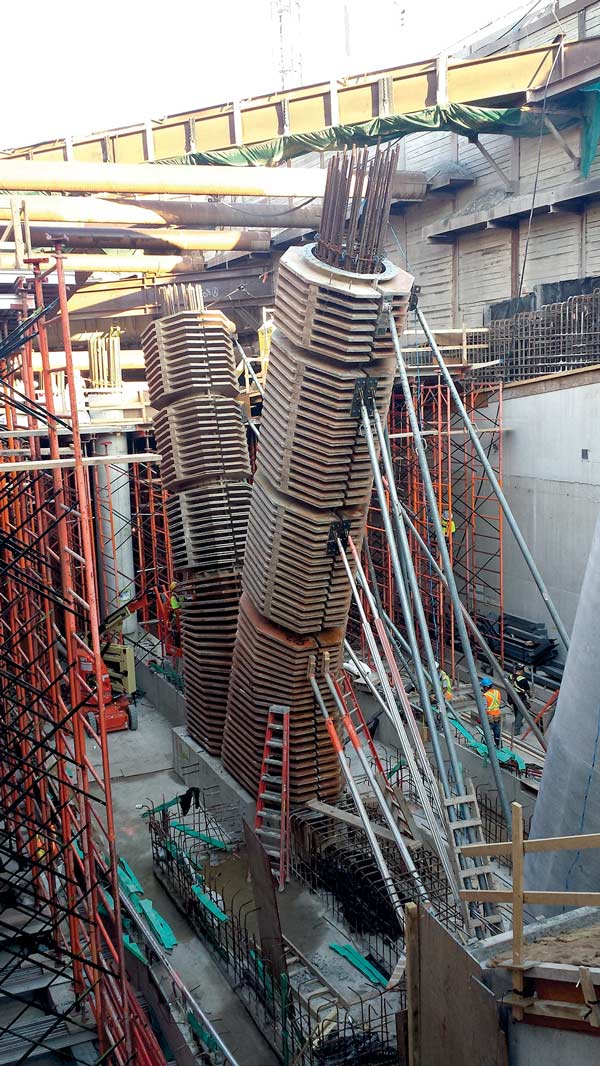
“We did some trial and error testing off-side to see what would work best,” Soleimani says. “We did some mock-ups before pouring the actual columns and went through a learning curve.
“And to ensure everything was seamless with the self-consolidating concrete, we used guillotine valves and poured from the bottom which turned out to be the best method. The fibreglass actually released really well and we got a good finish.”
The saddle was another challenge, he says. It’s a mass concrete curved ceiling spanning between both station entrances under Steeles Avenue West, some eight metres below grade.
It took 14 concrete pours of 700 to 1,100 cubic metres to accomplish using traditional wood forms and some loose filler.
“It runs about 150 metres by 90 metres with 2,800 square metres of exposed surface,” Soleimani says noting the height varies from 9 metres at the peak down to six metres and is about two metres thick.
“The trick there was to ensure the rebar didn’t sink into the concrete and stayed in place,” he says.
The third concrete challenge was the rock-wall, which runs at the station’s south concourse and required some special Styrofoam forms to get some 350 points of intersection accurately laid out using GPS to line them up.
Styrofoam was the only material which would give the unique geometrical shapes required for the angle of intersection, Soleimani says.
Again the forms were designed using 3D CAD (computer-aided design) software and put in place before an architectural mix of 10 mm (pea gravel) aggregate with a 750 mm spread rating was poured, again using a guillotine valve.
“Of course with the Styrofoam, we couldn’t vibrate the forms during the pour because we would damage them,” he says noting the mix was also quick-set so once they started pumping they couldn’t stop because the goal was a smooth, seamless finish with no visible lines.
General contractor Walsh had to manage a ballet of trucks in and out to keep the concrete flowing with two pumps simultaneously and back-ups on stand-by.
Releasing the Styrofoam once the pour was completed became the next challenge and the organic solution, using vegetable oil as a barrier, wasn’t overly effective.
“We couldn’t use chemicals because that would cause problems with the Styrofoam,” Soleimani says.
To resolve the residue left by the vegetable oil crews sanded the surface to create a smooth, contiguous finish.
“The rock-wall is a very interesting architectural feature but it’s the one we had the most difficulty with in terms of a forming system,” he says noting joints were buried into intersection corners to keep everything seamless.
“We had the Styrofoam forms made with a CNC (computer numerical control) machine based on 3D plans. The wall is 50 metres long and four metres high and we needed to have no seams.”
There were a few sleepless nights because of the challenges but ultimately the concrete was poured and all stakeholders were happy, and that, says Soleimani, is what matters.
Recent Comments
comments for this post are closed