New elevator technology that may be ready for market in five years will not only transform how people move within tall buildings but it also has the potential to revolutionize the shape and functioning of many high-density urban forms.
So say spokespeople for Germany’s ThyssenKrupp, whose new magnetized MULTI system will enable architects and engineers to shed the cable systems that restrict people-moving in today’s skyscrapers.
The MULTI system, using the same linear motor technology that moves the magnetic levitation train Transrapid, will permit the use of multiple cabins in one shaft, with no limits on height travelled and enable horizontal as well as vertical transport, turning elevators into multi-directional metro systems.
The new technology was announced a year ago by ThyssenKrupp. On Nov. 5 the firm unveiled a fully functioning scale model at its Innovation Centre in Gijon, Spain.
In announcing the latest development, Andreas Schierenbeck, CEO of ThyssenKrupp Elevator, said, "Our research and development team is right on track to realize this cutting-edge transport technology. MULTI will be our answer to tomorrow’s challenges."
ThyssenKrupp’s head of media relations Michael Ridder expanded upon the firm’s plans in exchanges with the Daily Commercial News, saying that industry demand for better people-moving systems played a large part in the firm’s drive to expedite bringing the MULTI to market; that the ThyssenKrupp is working with 30 potential clients around the world who are interested in the MULTI system; and that based on their calculations, "we will have the MULTI ready for the market by the end of 2020."
The introduction of cables to lift elevators by Elisha Graves Otis in 1853 heralded a new era in the building of tall structures.
Now, "the MULTI will be a game changer for the elevator industry as well as the building market. It opens up new possibilities for visionary ideas and concepts and it will enable new sizes, shapes and forms of buildings," said Ridder.
Using steel cables, elevators had topped out at about 500 metres per vertical run due to the weight of the cables, meaning that today’s skyscrapers that exceed that height need two stages of elevators (the Burj Khalifa of Dubai is currently the world’s tallest building at 830 metres, of which 585 metres are occupied). A recent breakthrough came last year, when KONE of Finland announced the development of a new lightweight material known as UltraRope that it says will enable elevators to travel one kilometre continuously.
The MULTI, with its multiple cars per shaft (meaning there will always be a cabin ready, within 15 to 30 seconds at all times, it is estimated), increased transport capacities, unlimited height, reduced elevator footprint and three-dimensional directional capabilities, takes elevators and thus buildings themselves the next step.
ThyssenKrupp introduced its TWIN elevator technology that prevents cabins from getting too close to each other inside shafts 10 years ago and has announced that the MULTI will use new lightweight carbon composite materials for cabins and doors, weighing 50 kg instead of the 300 kg in standard elevators, resulting in an overall 50 per cent weight reduction.
Ridder says ThyssenKrupp spends 700-million euros — almost a billion Canadian dollars — on research and development per year (2013-2014 figures).
Rival elevator companies Otis and KONE were contacted to discuss magnetized movement for elevators. Otis declined comment. Patrick O’Connell, director of marketing and communications at KONE, issued a statement:
"We have also maintained R&D projects on the magnetic movement concept for decades. We do believe buildings will feature multi-car and rope-less elevators in the future, however this technology is not yet technically or commercially viable."
The next stage for ThyssenKrupp, beyond the scale test model now in operation which has two 10-metre shafts and four cabs, will be further testing in a 246-metre Test Tower currently being built in Rottweil, Germany. It will be operational in 2016 and open to the public. The Test Tower will have 12 test shafts including three dedicated to testing and certifying the MULTI system.
Certification of new elevator technology like the MULTI for use requires the manufacturer to follow a methodology established by the American Society of Mechanical Engineers, explains Lynn Ramsay, communications advisor at Ontario’s Technical Standards and Safety Authority (TSSA).
A certificate of conformance would have to be obtained from one of two worldwide Accredited Elevator/Escalator Certification Organizations. The certificate would then be presented to technical bodies such as Ontario’s TSSA in local jurisdictions for final review.
"Over the last decades elevators became the bottleneck in the evolution of the architecture of buildings," said Ridder.
"So over the years customers approached us again and again, asking for more flexible solutions. Now it’s our turn to engage our customers to finalize this innovation together."
With a smaller footprint for elevator systems, and more, lighter cabins per shaft, there will not only be energy savings but cost savings for building developers, Ridder explained.
"The immediate benefit for the investors by gained floor space over the building height of 100 and more storeys is much higher than the initial investment cost for the elevator system," he said.
"It is too early to give detailed product price indications, but it is very clear that the savings in reduced footprint for super tall buildings is enormous and pays off easily."
A video showing the technology is availble on YouTube.
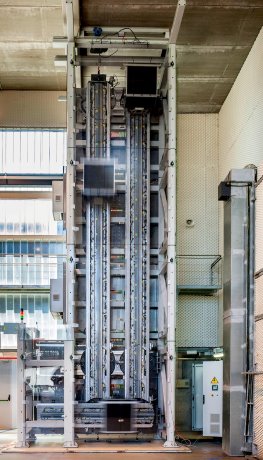
Pictured above is a scale model of the magnetized MULTI elevator system from ThyssenKrupp that was unveiled Nov. 5 in Gijon, Spain. The test model features two 10-metre shafts and four cabs.
Photo: ThyssenKrupp"
Recent Comments
comments for this post are closed