When the skill of the construction team bringing in mega-project Marine Gateway is drilled down to one feat, it is the ability to raise up a project with two residential towers only yards from an operating rapid-transit line and a commercial and office tower over a busy bus loop serving South Vancouver.
"We actually built underneath the (Canada Line) guide-way on the north side and connected into the station on the south side so that people (in the residential towers) living there don’t have to go outside," said Ledcor Construction Limited project manager Crystal Schroeder, who worked the project with senior project manager Jonathan Boyce and senior superintendent Carlos Perdomo.
The project has earned three members of the construction team silver awards of excellence from the Vancouver Regional Construction Association. They are Ledcor in the category of general contractor on a project valued at over $45 million, Keith Panel Systems Co. Ltd. in the category of a trade contractor working on a project valued at over $8 million and Mott Electric General Partnership in the category of electrical contractor on a project valued at over $8 million.
Marine Gateway, which is a $372 million, mixed-use, 1.5 million square foot development, sits on 3.5 acres on the south corner of Marine Drive and Cambie Street. It is comprised of five below-grade floors (four and a half are parkade), two residential towers (461 units) on the west side and a 15-storey office tower on the east side. The residential and office towers top 240,000 square feet of retail space with 30 outlets and an 11-screen Cineplex theatre complex.
Cutting between the east and west towers is a concourse to retail stores. On the west side, the northern residential tower is 38 storeys while the southern residential tower rises up 29 storeys with both towers connected on the first four levels. The two towers are six feet from the Canada Line.
Building towers a mere two yards from the Canada Line prompted Ledcor to devise new strategies to prevent debris falling onto the guide-way. Ledcor developed and implemented a debris control plan and a Clean-as-You-Go program that removed any debris from the area. Schroeder said the debris control program was incorporated into the safety training to emphasize the needed care to prevent any debris falling onto the guide-way.
Although vertical netting was in place, construction crew members working in that area had tools and even hardhats attached by lanyards to their body or to the structure to ensure anything that was blown by winds or dropped didn’t land below. Ledcor also placed waste bins throughout the site and workers cleaned their areas of debris and materials as they worked.
This plan and program were presented to TransLink and reviewed on a daily basis to ensure that all materials, no matter how small, stayed on site. TransLink now uses the program as a benchmark for other sites where construction is occurring.
The project also required excavating 60 feet into the ground directly beside the Canada Line station, requiring a special anchor design to ensure the station’s foundations and guide-way remained stable. Daily survey monitoring was carried out.
As the structure came out of the ground, TransLink operator Protrans requested permanent housings be designed and installed over the station’s two tracks (one going south and the other going north) by the residential towers.
"Without this, we would have had to stop construction," said Schroeder. While the housing captured debris landing on the station and guide-way during construction it was a permanent structure to deflect any items tossed or accidently dropped from the buildings once occupied.
"We quickly figured out a design and got the roof in place," explained Schroeder.
The steel structure with aluminum grating was installed between the hours of 1:30-4:30 a.m. when the trains were not running. The structure was prefabricated off-site and tower cranes were used to install the sections.
Keith Panel Systems (KPS) was responsible for engineering, fabricating and installing over 200,000 square feet of façade product throughout the complex, including the towers on the side of Canada Line. The scope of work included the building’s rain screen, sub-grid material and insulation.
"We worked directly above the Canada Line and on a tight schedule," said KPS senior operations manager Garry Wong.
Wong said one of the challenges the company met was ensuring that that material placed on the buildings throughout the complex corresponded with the building design. A walk through the massive complex shows the many different surfaces broken by doorways, escalators, retail outlets, patios and walkways. Wong said KPS was able to fabricate within its plant, the material to fit precisely these areas.
"You didn’t want to finish an area with half a tile," he said.
KPS also looked at ways of achieving value engineering in materials and manpower deployment. The company was able to find an alternative to frittered glass in the form of custom green aluminum composite panels with a "Spectra" finish that provides an equally brilliant high gloss. The Spectra product saved dollars for the client. Other notable cost savings included engineering extruded aluminum architectural grilles that appeared similar to the specified terracotta grilles. KPS also replicated sunscreen profiles using an alternate, folded aluminum composite material. Several other innovative techniques were used such as optimizing panel sizes to yield the greatest efficiency in material usage and labour time.
KPS maximized manpower on site by working on balconies and in alternate areas when concrete was being poured for the floor slabs on buildings and saved an estimated six months in work time. The KPS field crew of 40 installers finished the project in 15 months. The project was the largest value-engineering exercise undertaken by KPS.
Marine Gateway is designed to meet the new ASHRAE light conservation requirements for new construction. Ron Helmer of Mott Electric said that required the parkade lights to be turned off when no one was in the various areas of the four and a half levels of underground parkade.
"We had to come up with innovative ways to deal with this," he said, adding that it had to be done economically.
The project was one of the largest that Mott had undertaken as it provided the electrical service for all three towers, the power supply to retail outlets and the plaza areas which feature festoon lighting, plus the parkade, fire alarms and 28 elevators serving the complex.
"It was phased occupancy," Helmer said of the residential towers and the developer had to meet commitments to buyers and that placed pressure on the Mott crew to ensure those units were ready.
The residential towers couldn’t be occupied until the fire alarm system was installed. "The alarm system is so huge (in the whole complex) that there are four separate report points for the fire department," he said, adding the system is like four fire alarm systems but merged to one.
"We had a dream team, you couldn’t have asked for a better electrical team. They put their heart and soul into the project and worked overtime near the end (on the fire alarm system)." he said.
Helmer said the challenges were constant during the project as the massive site had multiple buildings that were built simultaneously.
"Everything went at the same time," said Helmer, as the towers raised almost "pyramid" style with crews filling in the spaces as the project continued.
As concrete slabs were placed and joined to the next one, it required that the conduits for electrical be placed precisely. Mott used AutoCAD for the design’s conduit placement but on site used Trimble, which integrates a wide range of positioning technologies and can take those points and easily map them.
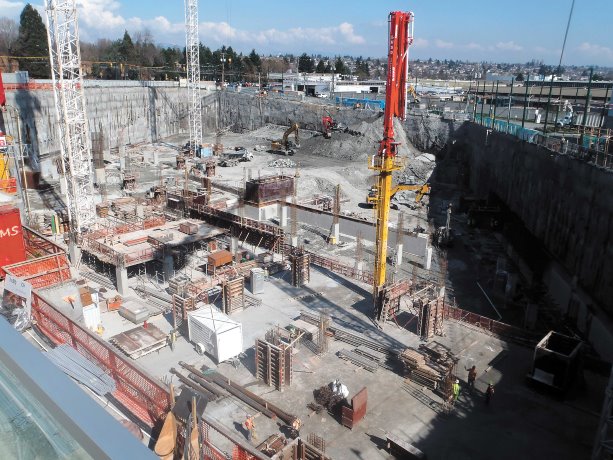
1/2
Mega-project Marine Gateway is a mixed-use development on the south slope of Vancouver at the foot of the Cambie corridor. Marine Gateway consists of 1.5 million square feet of development with one office tower, 30 retail outlets, and two residential towers, all built next to the Canada Line station and a bus loop.
Photo: Photos courtesy of VRCA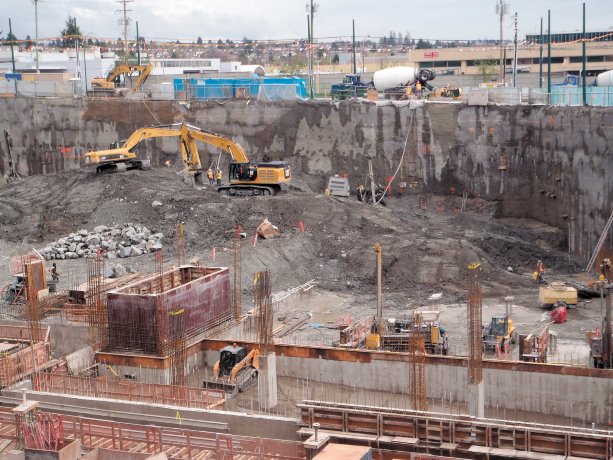
Recent Comments
comments for this post are closed