Jacobs has won an Award of Excellence from the Association of Consulting Engineering Companies – British Columbia in the 2024 municipal and civil infrastructure category.
The company won for civil engineering, rehabilitation and design and engineering services during construction of the New Westminster Interceptor Columbia Section Rehabilitation project.
Jacobs’s client on the project is Metro Vancouver.
“We were proud to hear that we won the 2024 Award of Excellence,” says Yariv Ben-Shooshan, senior project manager, water and wastewater at Jacobs. “The project is unique, especially in the Lower Mainland.”
The New Westminster interceptor, which was built in 1971, is a key piece of Metro’s sewer system.
It processes around 264,000 gallons of wastewater that is produced by 2.7 million residents every day.

It processes around 264,000 gallons of wastewater that is produced by 2.7 million residents every day. After a 20-year series of temporary repairs on the Columbia Street stretch of the interceptor, Metro engaged Jacobs to rehabilitate the deteriorating sewer, restore its structural and operational integrity, meet future flows and provide a barrier against future corrosion.
A 1.6-kilometre portion of it runs below New Westminster’s busy Columbia Street, the city’s main commercial hub and a designated historical district.
An interceptor sewer is a major sewer line that receives flows from trunk sewer lines.
“This flow is then directed to a wastewater treatment facility or another interceptor,” says Ben-Shooshan.
In a typical system, sewage first flows from domestic buildings in relatively small pipelines called laterals.
These pipelines take wastewater from residential and other private properties and direct it to local sewer lines that run under streets and other rights-of-way.
Local sewer lines then discharge the wastewater by force of gravity to trunk sewers.
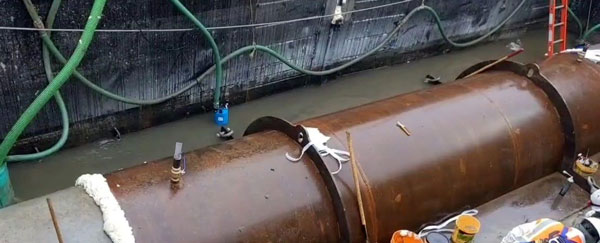
Finally, interceptor sewers take the contents of the trunk sewers and direct them to a treatment facility.
“Because interceptor sewers take collective flows from laterals, local lines and trunk sewers, they are among the largest pipes in a sewer network,” says Ben-Shooshan. “In our case, the interceptor was generally between one metre and 1.5 metres in diameter, conveying sewage collected from local municipalities.”
After a 20-year series of temporary repairs on the Columbia Street stretch of the interceptor, Metro engaged Jacobs to rehabilitate the deteriorating sewer, restore its structural and operational integrity, meet future flows and provide a barrier against future corrosion.
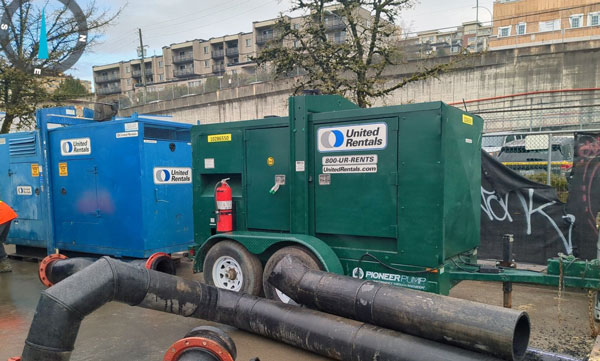
“The sewer was getting old,” says Colin Meldrum, director of engineering design and construction with Metro’s liquid waste services. “The sewage gives off hydrogen sulphide gases into the sewer. When the gases meet with the moisture of the sewer they form sulphuric acid, which eats away at the concrete in the pipes.”
Metro worked with Jacobs to develop a rehabilitation program for the Columbia Street interceptor that met engineering and operational requirements, was feasible to construct and was mindful of public impacts.
After evaluating several different approaches, Jacobs recommended live slip-lining.
Slip-lining is a trenchless technology for repairing leaks or restoring structural stability to a pipe in the ground.
It involves installing a smaller, carrier pipe into a larger host pipe, grouting the annular space between the two pipes and sealing the ends.
Slip-lining requires less digging and is often faster than other repair methods.“It is called live slip-lining because the sewage keeps flowing while the work is being done,” says Ben-Shooshan. “The flow of the sewage is used to float the liner and reduce friction when inserting the pipe.”
The Columba Street interceptor required live slip-lining in extreme hydraulic conditions that are not typical in pipe rehabilitation, with peak flow velocities in the order of six metres per second along the alignment and prolonged periods of surcharge conditions – when the sewer is under hydraulic pressure – in which the surcharge was metres higher than the surrounding surface level.
The interceptor rehabilitation project was the largest diameter and longest distance live slip-lining undertaking in the region to date in the Lower Mainland, says Ben-Shooshan.
Slip-lining rehab of the Columbia Street interceptor provided a number of benefits.
It took more than 1,000 trucks off the road, reducing earthworks and hauling, saving hundreds of thousands of gallons of diesel, and mitigating over 600 tons of CO₂ emissions.
In addition, slip-lining, rather than traditional open-cut construction, meant the sewer pipe didn’t have to be decommissioned and relocated, which would have created more emissions.
Live slip-lining in a high-velocity working sewer pipe required mitigation measures to prevent a possible sewer collapse: Emergency sewer closure systems, construction traffic loading management and overlapping design and procurement timelines to save time.
Ben-Shooshan says he thinks there will be more rehabilitation in the future, due to aging infrastructure and a lack of space for new utilities.
“In addition, rehabilitation is generally less disruptive than open-cut installation, because it requires excavation only at pits and maintenance holes,” he says. “Rehabilitation enables infrastructure to be restored both structurally and operationally and its service life extended to where it’s similar to new infrastructure.”
Recent Comments