The Dynamic Beast — a heavyweight in the world of crane barges — has been instrumental in the final leg of assembly of the new Johnson Street Bridge spanning the narrows between Victoria’s Inner and Upper Harbours.
Set to open in April, the lift bridge is a single-leaf bascule design with a 46-metre-long deck that will carry three vehicle lanes and provide equivalent space for bicycles and pedestrians.
The deck and bascule leaf, which is the pivoting device to lift the bridge deck, were assembled on the huge barge and then hoisted by the crane into place, a job few cranes in the world can do.
Normally, the deck and leaf would have been built in-situ but construction activity and the busy navigational channel would have hampered the assembly schedule, driving up costs, says Jonathan Huggett, engineer and the bridge’s project director for the City of Victoria.
The Dynamic Beast, which has the largest lift capacity on the West Coast of North America, was supplied by Vancouver-based Dynamic Heavy Lift Equipment.
The bridge design is novel. There is only one other single-leaf bascule design like it, “a much smaller” crossing in London, England, says Huggett.
“The characteristics of this bridge are it doesn’t have an axle around which it rotates. It sits in a cradle and the whole thing opens up,” he adds.
Hydraulic motors turn drive shafts that engage gears that turn the 290-tonne rings to raise and lower the bascule span, he says. Each ring is supported and rolls on two assemblies called equalizers.
“One of the features the architect (WilkinsonEyre, of London, England) came up with allows pedestrians to walk through the rings and see the bridge actually at work opening and closing,” he says.
The project director, who has experience on projects costing more than $1 billion, including Vancouver’s SkyTrain, calls the $105-million bridge “far and away the most complex” project of his career.
“People always say to me, ‘It’s just a bridge,’ ” says Huggett, who calls it a complex piece of machinery “because the whole thing opens and closes. I have been quoted in the media as saying, ‘It is more like a Swiss watch than a bridge.’ ”
Huggett says one of the challenges has been to meet “incredibly tight dimensional tolerances: It only works if it is built very precisely.”
He credits general contractor PCL Constructors Westcoast for building the structure to the specified tight tolerances.
Huggett was first invited to consult on the project more than five years ago and expected to be on the job for only a month or so. He says the complex design has seen a number of delays. A major one was in 2015 when bridge steel manufactured in China was rejected because it did not meet design specifications.
The new crossing features a steel orthotropic deck with a road surface made of epoxy applied directly onto the steel deck.
The crossing will replace the adjacent lift bridge, which is nearly a century old. While critics suggested rehabilitating the original Johnson Street Bridge would have cost less, Huggett says to meet new seismic code standards, as Victoria has the highest seismic risk in Canada, a new bridge made sense.
Furthermore, rehabilitation work would be beset with unknowns, making it difficult to come up with an accurate costing, he says.
Huggett says the bridge crosses over a very busy channel and many of the marine vessels are up to 6,000 tonnes and “barely able to squeeze” through to get to a nearby busy shipyard and other industrial operations.
“One of the challenges is making sure the bridge is properly protected” from being hit by marine traffic, he says, noting fenders will be installed along the bridge to prevent damage.
The bridge’s consulting engineer is WSP. Hardesty & Hanover of New York designed the steel work for the crossing.
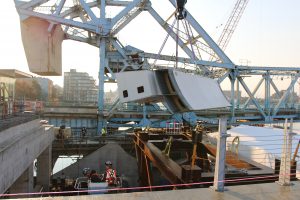
Recent Comments
comments for this post are closed