The new Chartwell Retirement Residences headquarters is the first office building in Mississauga, Ont. to use BubbleDeck technology to create interior open spaces with unobstructed views.
BubbleDeck uses a technique of linking air, steel and concrete in a two-way structural slab, explains the company’s website. Hollow balls made of plastic recycled from kayaks and canoes are inserted into the slab and held in place by reinforcing steel. BubbleDeck saves weight in the middle of the slab between the columns by creating a “concrete honeycomb.”
“If the philosophy of space and usage of space dictates that you have to have an airy feeling and have it open, then BubbleDeck certainly does do the job,” said Milan Azanjac, project manager, buildings for Maple Reinders Constructors, who is the general contractor for the build.
He added BubbleDeck is used in a lot of educational institutions for lecture halls.
“In order to achieve that you can’t really have vertical obstructions like columns…the purpose of the hollow bubbles is to alleviate weight so the further you go towards the middle of the slab, that’s where the bubbles do their trick and allows for your slab not to be heaviest at the midpoint,” he explained. “Then you’re able to have greater spans between your columns.”
The architect on the project is Sweeny &Co. Architects Inc. and the structural engineer is Blackwell, the exclusive partner of BubbleDeck in Canada.
The benefits of the technology include a reduction in the use of structural concrete, creating a lighter, thinner slab and a reduction in the use of formwork.
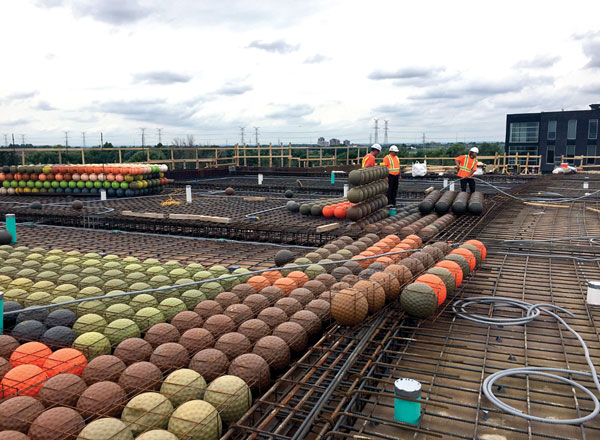
The use of air in the bubbles also provides additional benefits including thermal isolation and building noise reduction, the company states.
For the Chartwell headquarters, Azanjac explained, the designer and the clients wanted a training kitchen for their cooks to be an open space with unobstructed views.
The plastic balls, or bubbles, come from a manufacturer in Brampton, Ont. The balls are sent to Pittsburgh, Pa. where they are put into metal cages. The cages were then shipped to the site and installed.
Installation is the same as any other cast-in-place method, Azanjac said.
“The only difference here is that once you put the bottom mat of rebar then the bubbles come in and the bubbles create those voids,” said Azanjac. “Then mechanical and electrical conduits and knockouts are placed, followed by top mat of rebar prior to concrete being poured.”
The concrete is solid near the columns where the connection needs to be strongest.
“The only areas where you do not have bubbles usually is around your columns,” Azanjac noted. “They actually remove the bubbles and there you would have solid concrete like you would in your regular cast-in-place suspended slabs…to stiffen the slab in that area.”
There are some challenges when pouring the concrete using BubbleDeck as opposed to conventional slabs. More supervision is needed to ensure quality, he said.
“The balls are spherical and buoyant, so if you put too much concrete the first time there is nothing preventing those balls from just floating up,” said Azanjac. “You have to pour the first two or three inches and vibrate all of that, let it set a little bit without forming a cold joint and then pour the remainder on top. It’s a little more labour intensive and it does require some prep but in the pre-pour meetings that our site supers did with the trades and the quality control assurance that we had throughout the process we didn’t really have any issues.”
The system saves on concrete because there are air gaps inside of the slab.
“On Chartwell we had 5,900 bubbles that were 12 inches and 660 bubbles that were 16 inches in diameter,” said Azanjac. “We were able to save 472 cubic yards of concrete which is equivalent to 60 concrete mixer loads approximately. The total weight saved was approximately 318 tonnes.”
Another important aspect is the environmental benefits.
“It’s a very innovative idea that has a lot of benefits for the environment,” stated Derek Bunting, regional manager, buildings with Maple Reinders. “We’re using recycled plastic which is very important for the environment, the reduction of the concrete trucks and the impact of all the trucks coming to site and the pollution.”
While the cost is a little more than traditional construction, the benefit is the functional space it provides for the client, Azanjac added.
“I believe it was five to 10 per cent cheaper when we did the calculations but then the space itself wouldn’t have the same feel and the same purpose to what the client and architect wanted,” he said.
Furthermore, because it’s hollow, it reduces vibration in any building between the floors and both airborne and contact noise by as much as 200 per cent over a conventional solid slab.
Recent Comments