Safety and production have been top priorities in the development of concrete core climbing systems over the past decade and nowhere is that more on show in Canada than downtown Toronto.
A case in point is an electric formwork climbing system, the first of its kind in Canada, being used for the concrete core of a structural steel framed 45-floor office building on Front Street.
Made by M-Tech, the climber jumps an entire floor of the concrete elevator core at once. That differs from hydraulic climbers, which are commonplace in Toronto, that only jump segments of a floor of the core at a time, explains Kevin Nagowski, project manager, Alliance Forming Ltd., the forming contractor for the office tower.
Another reason Alliance chose the electric climber is worker safety, he says.
“We have eliminated the leading edges that you have with other systems which jump separately…creating fall hazards,” he says.
A feature of the system is the location of the electric motor and other moving parts at the top of the climber where they are easily accessible if repairs are required.
“If something goes wrong, we can literally unbolt it right from the top of the tower crane, lift it up and change the main motor out in 10 minutes,” Nagowski says.
By comparison, the hydraulics and mechanicals of conventional climbers are difficult to access for repairs, he points out.
The M-Tech climber is also easy to move because there is no hydraulic system bolted into the elevator core.
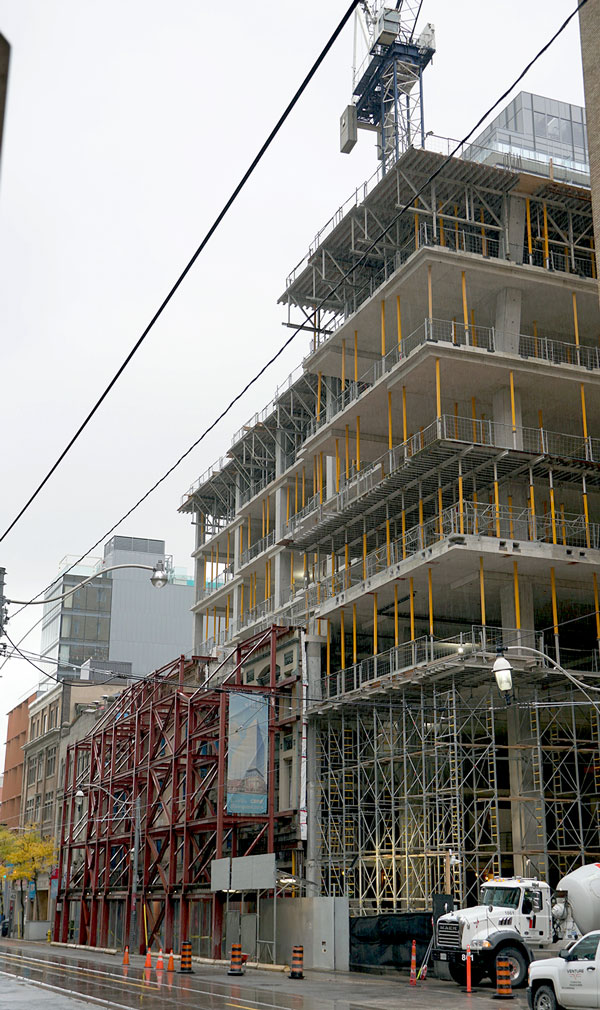
Denis Furlan, director of Alliance, says he would not hesitate to use the electric system on another structural steel tower.
He points out the climber is best suited to towers at least 25 storeys tall.
Just a few blocks away in downtown Toronto is a concrete cast-in-place 18-storey tower under construction for Google. The climber there does not require a crane when it carries the exterior coating panels for the concrete elevator core.
While the benefit of the FCI Self Climbing System by Aluma Systems is that it frees the tower crane for other tasks, the self climber also “frees up real estate” on the tight site, explains Joe Plantamura, general superintendent with Structform International Limited, the formwork contractor for the project on King Street East.
“Real estate is very important in downtown Toronto,” says Plantamura. “I don’t have to take the forms off and look for a place to store them.”
Another advantage to the climber’s design is that it is less labour intensive than some climbers.
“I have eight men (carpenters) working on the core.”
Some systems would require twice as many workers, he points out.
Plantamura says it takes about four hours to strip it, remove all bolts and attachments to the concrete core, and another hour to climb to the next floor.
For experienced workers and foremen, he adds, “it is pretty easy to put together.”
At Bay and Adelaide Streets in downtown Toronto the 32-storey Scotiabank North Tower is rising with a hydraulic climbing system made by Doka.
It is the second time the Doka climber, which consists of three integrated systems, has been used in Toronto by Structform. The first was the recently completed CIBC Square on Bay Street where Doka was customized to complete the 54 floors in only 36 jumps, says Leo Bahou, general superintendent of Structform.
“It is a unique animal, designed to beat the schedule,” he says.
Horacio Leal, business representative of Carpenters’ Local 27, has witnessed the three systems at work and says Local 27 carpenters on the sites are working with high-production climbers without sacrificing safety standards.
He says he has seen significant improvements in climbers in Toronto over the past 15 or so years.
Expect Toronto to continue to be at the forefront of the new technology, says Mike Yorke, president of the Carpenters’ District Council of Ontario.
“The city is one of the global leaders in the commercial development sector and here is an example of where we are leading on technology and new systems,” he says, adding that the new climbing technology “meshes well” with the Carpenters’ formwork training programs for the next generation of carpenters.
Recent Comments
comments for this post are closed