This summer a superstructure for a four-storey housing complex will rise on a former public parking lot in Toronto’s Kensington Market.
What is novel about the 78-unit affordable housing project is that, other than a concrete foundation, it will be constructed of cross-laminated timber (CLT), including the elevator core.
Design firm Montgomery Sisam Architects chose a CLT superstructure (floors, roof, exterior walls) partly because it can be erected by a single trade in six to eight weeks, rather than the months required for conventional concrete construction, says Daniel Ling, a principal of Montgomery Sisam.
The complex, which is being built under the City of Toronto’s Rapid Housing Initiative phase three, also earns sustainability credentials. The embodied carbon intensity targeted for the CLT exceeds the “extra-low emission requirements” under the Toronto Green Standard.
“We’re dealing with the climate issue where construction and operation (of buildings) are one of the greatest emitters of greenhouse gas,” says Ling.
The Gillam Group is the design builder for the project on Bellevue Avenue and the CLT is supplied by Element5.
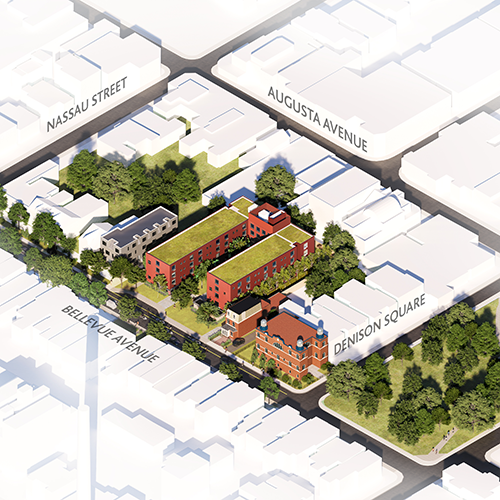
Kevin Hutchinson, principal at Montgomery Sisam, says mass timber was chosen over volumetric modular construction partly because of its design flexibility. It offers “more functional” floorplans for the one-bedroom suites.
The CLT elements are also easy to assemble onsite. Modular, by comparison, would require complex staging and hoisting into place, he adds.
“Generally it is a bit more challenging from a construction management perspective.”
In 2020, under phase one of Toronto’s Rapid Housing Initiative, Montgomery Sisam completed supportive housing using modular construction.
Ling, who doesn’t foresee any difficulties to the mass timber erection at Kensington Market, says site excavation has commenced and if the foundations and footings go smoothly the superstructure could be up this summer.
A “highly energy efficient building,” he says, it will have a building envelope rated to R-34 and a window-to-wall ratio of about 15 per cent.
It will be clad in a red standing seam metal siding, inspired by the character of the neighbourhood.
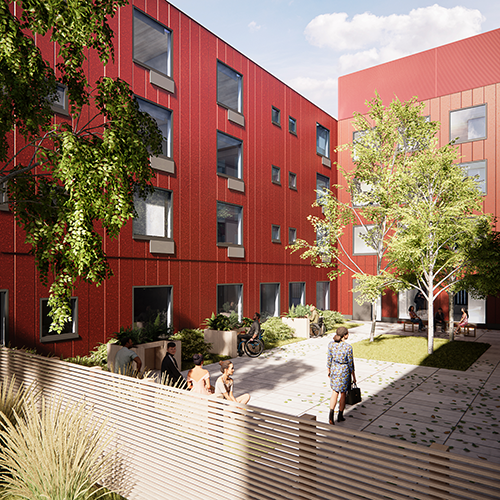
While the four-storey building is in a neighbourhood of single family housing, Ling says the design harmonizes with its neighbours because the U-shape form features a courtyard and the two 35-foot narrow ends of the building facing the street.
The U-shaped design also allows for more units than a traditional building design would on the lot, he says.
Trump’s tariffs on building materials should not impact construction costs because the subtrade packages were awarded last year.
“We do have other projects on the go where we are looking carefully at all-Canadian sourced products…The tariffs are definitely a concern and it takes an effort to minimize the impact.”
Montgomery Sisam has a handful of mass timber projects on the drawing board and others underway, including at the University of Toronto’s Koffler Scientific Reserve in King Township.
The firm is also designing an affordable housing complex in the Region of Durham which is comprised of a mass timber hybrid system that employs CLT slabs and panelized stick frame walls, says Ling.
“You gain some of the speed advantage (of mass timber) but you bring down some of the costs by using stick-built for the panels,” he says.
The Kensington Market project is being done under the City of Toronto’s City Builder initiative which simplifies rezoning and cuts months off the traditional zoning process, says Hutchinson.
All of the building’s deeply affordable units will have rents capped at no more than 30 per cent of each resident’s income. It will offer support services such as health care, meal programs and employment resources.
Hutchinson says more Ontario municipalities are incentivized to move quickly on non-market housing initiatives like the Kensington Market project.
Recent Comments