Designing a scaffolding system to rise 120 ft. at a 90-degree angle is easy enough for an experienced scaffold contractor — it is another story when that scaffolding soars on a tilt.
Such was the case near Sudbury, Ont. where Phoenix Industrial Services was retained to design and build a 120 by 65-foot wide tower of steel tubing up the side of a 90-year-old power dam undergoing a concrete repair and maintenance program last year.
“System scaffolding is very strong vertically, when you stand the tube legs vertically on top of each other,” says Andrew Smith, general manager, Phoenix Industrial Services.
At the power dam, however, Phoenix had to angle its scaffolding by as much as 15 degrees, off vertical.
In other words it rose 75 degrees, not 90 degrees up.
In the past, Phoenix has relied on conventional design methods to calculate a structurally sound tower on such an angled vertical rise. That can be time consuming.
On a previous project, for example, a tower scaffolding design was out by two or so degrees, explains Phoenix’s president Paul Lynds. “We had to re-adjust the whole scaffold . . . . order different sizes of ledgers to figure out the correct angle.”
With a tight schedule and budget at the power dam, Phoenix could not afford a trial and error process of assembly in-situ. Therefore, the contractor turned to a 3D modeling software program to ensure a properly engineer scaffolding tower that would conform precisely to the power dam’s concrete face.
“With the 3D software, we probably saved 35 man days,” says Smith.
Even with 3D software the design solution was not simple because the contractor relied on original drawings of the near-century-old dam which didn’t include buildings constructed later at its base. Phoenix took photographs from the top of the dam looking down on outbuildings and input the photos into the software program.
Phoenix used a custom method of tying its rosette scaffold system into near-vertical faces. The design transfers most of the load from the steel tubing system into the structure — in this case the concrete dam.
“Our system uses anchors, but it is the manner in which we use them to attach the scaffold to dam face that is unique,” explains Smith.
“You could say it allows us to convert a concrete wall into a giant scaffold tube.”
Another challenge for the contractor was “a nasty winter,” which resulted in ice buildup at the base of the scaffolding near the lake’s edge. A protective buffer of straw around the scaffolding prevented damage or movement of the tower.
With no road access, materials and equipment were transported on barges and boats across a lake to the site. “We probably had to cross back and forth 30-40 times,” says Lynds, because the site had no laydown space.
“Once we knew what our bay sizes (comprised of standards, ledgers and braces) were going to be, we were able to ship the required ratios and quantities to allow us to keep building. It was about managing the right sizes and the right time.”
The scaffolding contract was completed on schedule in about a month-and-a-half, including equipment and materials mobilization, says Smith, adding that the peak crew was seven carpenters.
The site posed safety risks for the crew, but Phoenix had no lost-time accidents and, in fact, has had no lost-time accidents since the firm was founded by Lynds in 2001.
Part of the reason for the unblemished safety record is because, along with implementing the standard core safety program, the contractor always sets up site-specific fall protection plans and other site-specific mitigation measures. Even rescue plans are made.
“We don’t go into a project without fully understanding the risks and finding a way to mitigate those risks,” says Smith.
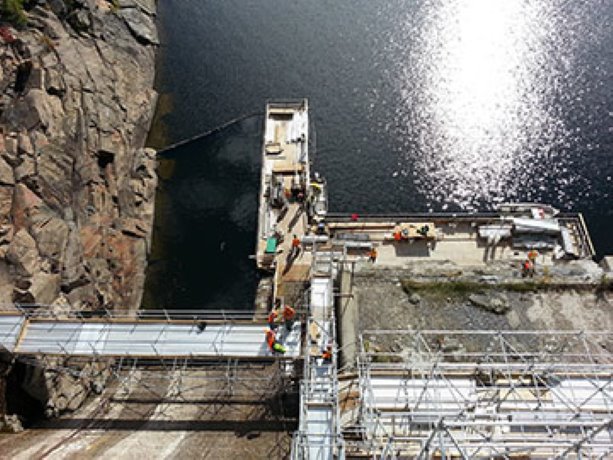
Recent Comments
comments for this post are closed