Meeting discharge water quality standards is an essential component of any construction project on Ontario waterways. The construction of a new 10-megawatt hydro power facility on the French River near its mouth at Lake Nipissing combined the challenges of eliminating a mysterious source of iron oxide with biting cold.
The Okikendawt Hydroelectric Project is a joint venture between Dokis First Nation and Hydromega Services. Miller Infrastructure Inc. provided drilling and blasting services in addition to concrete work for Hydromega, which acted as the constructor on the project.
“Miller called us when they were having difficulty finding the source of problems interfering with the discharge water quality standards set out by the Ontario Ministry of the Environment’s (MOE) Environmental Compliance Approval for the project,” says Jill Attwood, general manager of Groundwater Environmental Management Services (GEMS).
The project was designed to meet MOE’s criteria of Total Suspended Solids, turbidity, pH and ammonia. The most obvious visual problem at this point: the water had turned brown.
“The contractor had tried a variety of treatment methods but the efforts proved fruitless,” says Attwood. “When we came on the site, we tried a number of flocculants — chemicals that remove suspended particles — but they proved ineffective. That meant that the culprit was likely dissolved in the water. What was odd, was that the discolouration wasn’t there at the beginning of the project.”
Testing revealed that iron had been exposed when the contractor blasted bedrock in the river channel to create a new tailrace for the hydro facility. Exposure to air and water created the iron oxide that had discoloured the water. While the release of iron wasn’t an environmental concern, the discharge authorization required by Ontario Parks also stipulated that there was to be no visual change in water quality.
“This was all about aesthetics and iron is visible even at allowable quantities,” says Attwood.
Temperatures had already dropped to below freezing in November, limiting treatment options. GEMS calculated that the new tailrace was approximately 800 metres long, 18 metres wide and ranged from eight to 20 metres in depth.
“We believed that there was sufficient volume in the currently dry tailrace, that if we introduced clean water from downstream into the collected construction water prior to opening the water control dam, we could release water that offered no visual discolouration,” says Attwood.
Work proceeded at an accelerated 24-hour basis to complete construction within the tailrace, and to remove materials and construction equipment, leaving enough time to backflood the tailrace before the water control dam was opened due to emergency flood prevention requirements.
“The treatment solution worked, but we no longer had the luxury of using the tailrace backflow to deal with other isolated retention ponds used for construction of the powerhouse,” says Attwood. “We decided to treat the iron with limestone, which we had to ship to the site.”
Limestone was placed at the inlet of the lined containment pond where sumped water from the excavation was discharged. Granular limestone was not porous enough, and didn’t present enough surface area to absorb iron, so limestone rip rap — larger rock — was placed at the inlet, removing iron discolouration from released water.
As Christmas approached, temperatures plummeted, freezing equipment, hoses and the containment pond — to the bottom.
“A water level control dam was located next to the work area,” says Attwood. “It was like working in the mists of Niagara Falls at temperatures as low as -50 C. We were working in what amounted to a bedrock wind tunnel.”
GEMS first instructed the contractor to break open the ice surface of the containment pond with backhoes and excavators. Workers then installed glycol heating lines and a bubbler system powered by electric, oil-less compressors to prevent refreezing. The compressors themselves were placed in an insulated box equipped with a ceramic heater.
“Battling the cold and ice, we kept the containment pond ice-free and the discharge water clear,” says Attwood.
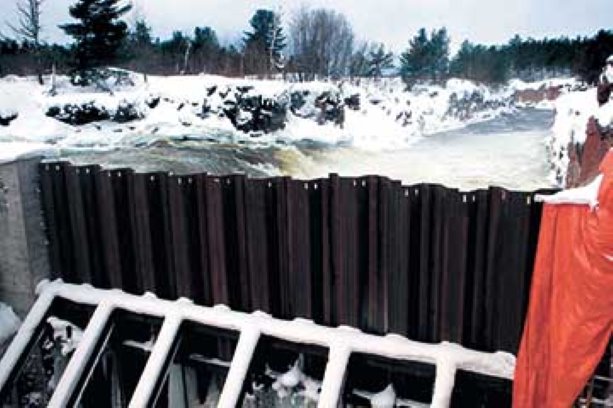
Recent Comments
comments for this post are closed