Aberfoyle Metal Treaters of Aberfoyle, Ontario provides heat treating for metal pieces as large as 400,000 lbs. some of its projects include the Rogers Centre in Toronto, formerly known as the SkyDome and home of the Toronto Raptors NBA basketball team and Blue Jays baseball team. Aberfoyle also worked on a pedestrian bridge over the mouth of the Humber River at Lake Ontario.
Vaulting steel structures often earn accolades for architects, engineers and builders. Rarely do metal treaters, who scientifically modify metal properties through the application of heat, receive credit.
Since 1989, Aberfoyle Metal Treaters of Aberfoyle, Ont. has specialized in large-scale heat-treating, servicing steel mills, foundries, and other industries such as nuclear power, hydroelectric, petrochemical, construction and heavy machinery. Some of its best known projects include Toronto’s Rogers Centre and the Humber Bay Arch pedestrian bridge.
The five-acre facility features a 100-ton crane and six furnaces that can be stoked to 2,250 Fahrenheit and provide heat treating for metal pieces as large as 400,000 lbs. The plant employs 28 workers.
“Our main furnace is the largest of its kind in North America at 82 feet in length,” says company president Harry Hall, who has been in heat treating since 1974.
“The furnace has guillotine doors on either end and two furnace car hearths totaling 164 feet, giving us the ability to heat treat even longer lengths than the chamber. If we’re heat treating a very long pressure vessel, the ASME code allows for a minimum five-foot overlap. By removing the vessel from the furnace and turning it 180 degrees before re-inserting it, we can achieve a 75 per cent overlap.”
The company’s industrial work includes components for nuclear reactors, hydroelectric dams, heat exchangers and large metal components for extraction of oil from Alberta’s Oilsands. Aberfoyle also heat treats massive axles for trucks involved in resource extraction.
The company is currently heat treating the tooling for the new Boeing 787 Dreamliner and the Airbus A350.
“The bodies of these aircraft are made of composites rather than aluminum,” says Hall.
“The material is lighter and more durable and the planes will fly at higher altitudes, but because the tools are so very large — up to 70 feet long by 16 feet wide and eight feet high — accuracy is critical.”
The company earned its reputation in aircraft tooling on the wing of a Boeing 747.
“When someone welds these components, there’s always the possibility of distortion during manufacturing,” says Hall.
“We set the tool up, laser level it and use a bit of a black art in putting extreme weights on these parts, and improving the straightness to within a quarter-inch of flatness over 60 to 70 feet of tool length.”
The company applied the same principle in straightening 400 ornamental metal castings used on the gates surrounding the Mosque of the Prophet Mohammed in the city of Medina, Saudi Arabia on behalf of Dominion Castings in Hamilton.
Aberfoyle also heat treated 5,000 tons of stainless steel billets for shipment to Dubai, used in making stainless steel rebar for some of its taller buildings.
“We bent the pipe for the Humber River pedestrian bridge in 1994,” says Hall.
“The bridge was designed but they were not yet sure how the bending of steel could be performed. The engineer asked us if we thought we could bend 48-inch diameter steel pipe into that extreme curvature,” says Hall.
“We achieved it by setting up a series of saddles underneath and above the straight pipe and left a gap where the pipe would bend to the specifications.We put on as much as 100 tons in weight, distributed along the length of the pipe. In some cases, we worked on a section two or three times.”
The company’s work on the Rogers Centre involved stress relieving a portion of the rectangular steel tubing in lengths of 40 to 60 feet to form the curvature of the dome’s roof.
“Anybody looking up at the roof would think the metal had been formed in a curve,” says Hall. “However, it’s all an illusion as it was all straight lengths of tubing.”
The company also operates a 15,000-square-foot metal blasting and coating facility, with contracts ranging from preparing communications towers and military structures, to the entranceway of a New York City hospital.
Last year, Hall was presented with the Heritage Award by the international Metal Treating Institute, an award offered only nine times since the organization was formed in 1933.
“When they called my name you could have knocked me off my feet,” says Hall.
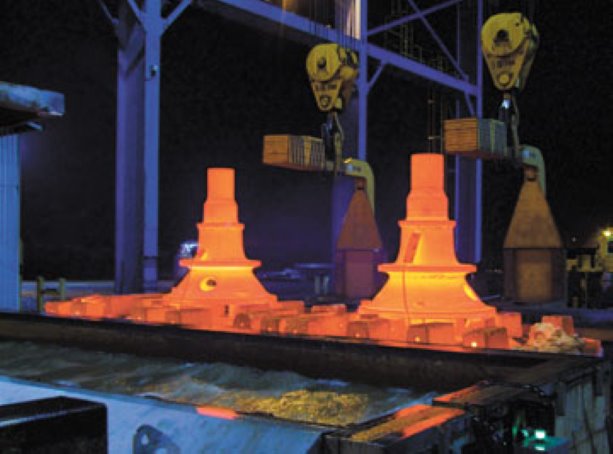
Recent Comments
comments for this post are closed