It’s not just another office building. Nor is it simply one building in one location.
Right from their conception, new quarters for the Wellington-Dufferin-Guelph Public Health unit were intended to address diverse needs ranging from providing space for community clinics, workshops and offices to vaccine storage and even a centre for emergency operations.
And right from the start, this ambitious, $24.4 million project, funded by the health unit, member municipalities and the provincial government, faced many challenges — one of which nearly succeeded in derailing it even before construction could begin.
The project began routinely enough, with planning activities such as a needs assessment, public consultation and search for appropriate locations, says Carole Desmeules, the health unit’s finance and corporate services director. Two sites were needed: one to serve Guelph and Wellington County; the other to serve Dufferin County.
The wide variety of activities the facilities had to host in turn prompted the need for some unusual requirements, such as equipping the buildings with their own generators to ensure an uninterrupted power supply, accommodating short wave radio communications that could be used in an emergency and even creating a safely sealed, negative pressure area to protect others from cases that might involve an airborne disease, such as tuberculosis.
“One of the important things was also public access,” says Desmeules. Meeting the province’s new guidelines for disability access, was yet another priority.
For Paul Sapunzi, a partner with +VG Architects (the Ventin Group Ltd.), an Ontario firm that is the project architect, the biggest challenge was therefore how to reconcile “all of these services and all of their special needs architecturally and put them into one place that can be intuitively understood by the community visiting the building.”
The solution, he says, particularly in the roughly 50,000-square-foot, three-storey Guelph facility, was to create a “commons in the centre of the building where visitors would have an intuitive sense of where services are being offered in the facility and be able to delineate between the more confidential private areas versus the more public areas” without having to rely on a lot of way finding or other methods to navigate.
“To me, the most successful buildings are the ones that take the most complicated program and create the most simple solution,” he explains.
By 2010 advanced planning had been completed and locations for the buildings found: leased land at a new University of Guelph research park for the Wellington-Guelph facility and a brownfield site in Orangeville’s downtown for the approximately 31,000-square-foot building that would serve Dufferin County residents.
The health unit’s board approved the plan. But expectations that the province would contribute substantially to the project failed to materialize (the province has since contributed nearly $4 million), and Guelph balked at its share of the cost.
A 2011 Ontario Superior Court of Justice decision upheld the health unit’s right to proceed and obtain funds from the city for the project, but the challenges were far from over.
Excavation at the Orangeville site, begun mid-November 2012, uncovered greater than expected soil contamination as well as the need to reinforce the foundation walls of century-old neighbouring buildings. These issues pushed construction back to January, says Christopher Guerra, a project manager for Concord, Ont.-based Buttcon Ltd., the project’s general contractor.
Guerra says adopting a construction management approach helped speed the work by allowing overlaps in design and construction phases. It also offered the flexibility of using “value engineering,” he says, enabling the team to identify the best cost-saving options that could be used to implement design specifics.
In Guelph, work began at the end of November 2012. Building on university land added another layer of requirements to be met on top of those stipulated by the city. These have ranged from having to comply with green space allocations to ensuring the use of natural materials in the building’s construction and meeting certain standards for its exterior look and energy efficiency.
“It was a fairly complex process to go through in order to meet all of the requirements of all of the parties,” Desmeules says.
Considerable effort has been made to seize the advantage of having two builds at once to improve economy of scale. Some sub-trades realized they could use the same crews on both sites, resulting in a cost savings for them “so they were able to offer aggressive pricing for us,” says Guerra.
Other synergies exist as well. For instance, the same architectural standards – such as lighting and mechanical systems – apply to both buildings. It not only means easier and more cost-effective maintenance, but also the creation of standards the health unit can apply to its several other locations in the region. They’ve standardized emergency control equipment across all of the health unit’s facilities, says Desmeules, as well as many other features like the security system and the vaccine monitoring system.
Knowing that a lot of construction would take place in winter, +VG opted to incorporate a steel structure with precast concrete floor slab for the Guelph building’s framework, says Guerra. “Which makes it a lot easier for us to construct through the wintertime as opposed to your standard ‘deck and pour’ construction,” he says. Precast floor slab was also used for the Orangeville structure, combined with concrete block walls.
By early December, the Orangeville building’s three floors were enclosed and watertight. Work on the exterior facade had begun; interior finishes were also underway.
At Guelph, the outside facade should be complete by mid-January, Guerra estimates. He explains the exterior is being enclosed floor by floor and as each one is enclosed the heat is turned on so work on interior finishes can begin. They are working from the bottom up.
Spring is the target for completion, with the goal of having the Orangeville building move-in ready by the end of April and the one in Guelph ready by the end of May.
The buildings have been built to meet LEED Silver certification, and their mechanical and electrical systems are designed to exceed OBC SB0-10 2012 requirements. Among the features that have helped to achieve the standard are internal water source heat pump systems, heat recovery from exhaust air, water-efficient plumbing, energy efficient LED and T5 lighting and plug load control in office areas.
The project remains on budget, but it hasn’t been easy, Desmeules admits, and credits the rigorous planning process ahead of the concept design for helping to keep the project so close to its targets.
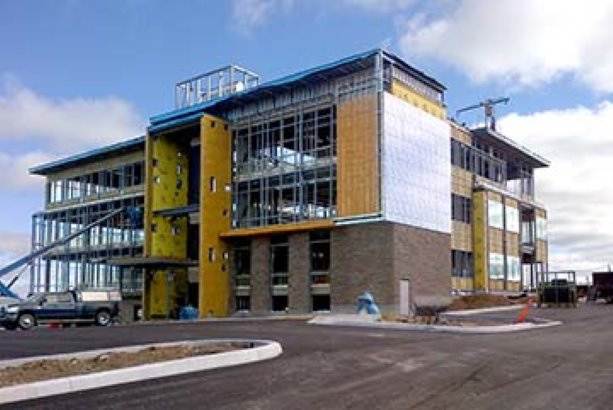
Recent Comments
comments for this post are closed