B.C. seems to be topping out when it comes to tall wood structures, with roughly 250 wood buildings built, under construction or planned in the province. At the University of B.C., an 18-storey student residence is touted to be one of the tallest wood buildings in the world, once complete in 2017.
As research and pilot projects push the boundaries, and heights, of wood highrises, a Buildex Vancouver session on Feb. 25 will explore the growing number of options.
"There’s been a lot of learning about what works best," said Graham Finch, a building science specialist and professional engineer with RDH Building Science. "Better practices for mid-rise and taller buildings has become a new area."
At his 90-minute, Best Practices for the Building Enclosures of Mid-Rise and Taller Wood Buildings, Finch intends to present the "nuts and bolts" about what’s unique about wood construction. "People associate wood framing with houses. This is beyond housing," Finch said from Vancouver.
Taller wood buildings, some up to 10 storeys and still standing today, were built before 1900, and later, but in the mid-1900s, national building and fire codes restricted wood buildings to three or four storeys. In the mid-1990s and early 2000s, Washington and Oregon allowed construction of five-storey wood frame buildings over concrete podiums.
In 2009, B.C. legalized five and six-storey wood-frame structures, followed by Quebec in 2013 and Ontario and Alberta in 2015.
While wood is viewed as a sustainable resource, and wood buildings are esthetically pleasing and can be built relatively quickly, there are obstacles, which include greater environmental loads from wind and rain, more rigorous energy code requirements and unique maintenance and operating considerations.
Because taller wood buildings face increased exposure to wind and rain, site protection becomes crucial, Finch said.
With increased height comes greater rain amounts at upper floors and cumulative run-down at lower levels, so water shedding becomes paramount.
A drained and ventilated rain screen is critical to control water penetration. Roofing, cladding, windows and other assemblies must be robust. Pre-fab components should be considered to hasten construction and reduce exposure to the elements. In Scandinavian countries, where a 14-storey tower was built in Norway, and an eight-storey building was constructed in Finland, it’s common practice to cover incomplete projects with a tent structure to keep the work-in-progress dry.
This isn’t normally done in Canada, Finch said, because of cost concerns. Instead, the building is left to dry in the open air, sometimes with risk.
He’s aware of situations in Western Canada where wood structures got too wet during construction which caused significant delays and larger costs because the wood had to dry.
Finch will discuss lessons learned from around the world as they relate to water management and cladding, air barrier strategies and materials, wood framing, energy codes and more efficient building enclosure assemblies and details.
In the last 15 years or so continuous advances related to building enclosures have occurred in the Pacific Northwest. One of the most significant changes, as a result of mandatory whole building testing in Washington State, has led to significant improvements in air barrier systems and details.
One of B.C.’s most talked-about wood buildings, the 29.5-metre tall, six-storey Wood Innovation and Design Centre in Prince George, opened in October 2014, and according to Finch, hasn’t developed any problems.
But, it’s Europe that has raised the bar when it comes to mid-to-tall wood buildings, Finch said.
In addition to having many companies that manufacture glulam, cross-laminated timber (CLT) and pre-fabricated components, Europe has a longer history of tall-wood construction.
In Canada, while there are several companies which produce CLT, glulam and other engineered wood products, the price of their products are higher than across the Atlantic. Still, mass timber products can be used to build a structure that’s just as durable and safe as a steel or concrete building, Finch said. "Wood versus other materials, it’s worth it," Finch said.
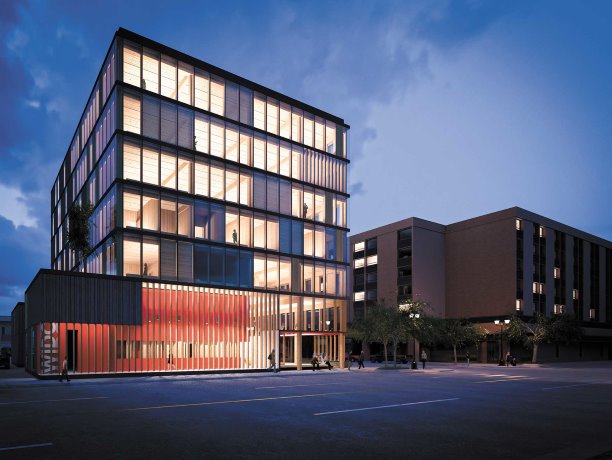
1/2
A rendering of the Wood Innovation and Design Centre located at the University of Northern British Columbia in downtown Prince George.
Photo: MGA Architecture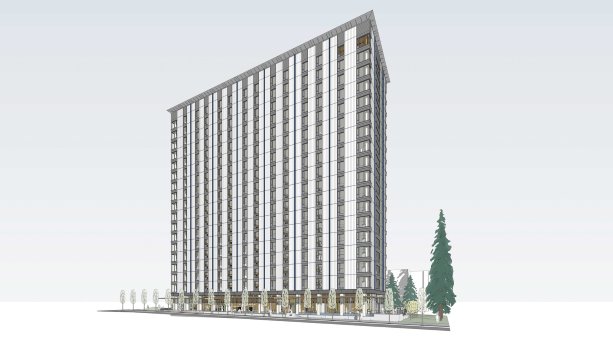
2/2
A rendering of the new 18-storey student residence tower planned for UBC
Recent Comments
comments for this post are closed