It’s not yet complete and already the building that will house the University of Western Ontario’s Ivey Business School is winning awards.
Ivey Business School substantially complete and a winner
It’s not yet complete and already the building that will house the University of Western Ontario’s Ivey Business School is winning awards.
The 274,000-square-foot gold LEED building in north London, Ont. nearly doubles the square footage of its predecessor, features five 50-seat classrooms, 15 78-seat classrooms, 112 faculty offices and many other meeting spaces, lounges and public spaces.
Earlier this year, the three-storey quadrangle strusign award of merit its architecture.
Architect Siamak Hariri, whose Toronto firm Hariri Pontarini Architects won an international competition for the design of the building, notes that his goal was to design a facility “to have atmosphere and to have spirit — that the very best candidate, be they students or faculty, walk in and say, ‘this is the place I want to be.’”
Integrating arecture and landscape so there is a seamless transition from interior to exterior space was another key goal, says Hariri. He maximized natural light in the interior on the main floor by adding glass walls to the meeting rooms that line a central courtyard and incorporating glass walls in the meeting rooms across the corridor from the courtyard facing rooms.
Low-e argon windows are used for the exterior walls of the building’s second and third floors as well as the walls facing the quadrangle and for skylights. A three-storey great hall that opens onto the quadrangle adds even greater access to natural light.
Natural materials, such as Douglas fir for ceiling timbers, walnut for inset benches and stone also predominate in the $110 million facility. Copper cladding adds a quiet contrast to stone on the exterior.
“We worked with Owen Sound Ledgerock to provide all of the stone for the building and we got them engaged very early in the process,” says Michael McLean, manager of planning and design in the university’s facilities management division.
The early involvement ensured the project’s schedule could be met.
Glen Armstrong, the university’s building project manager, notes that a lot of the stone destined for the interior required engineering and specialized machining at the quarry. A stone staircase, a main feature of the building’s great hall, was especially tricky to assemble. Its stair treads weighed between 200 and 300 pounds.
“It’s a lot of fine work and precise work using heavy materials,” he says.
The building’s development began in 2009 with the architectural design competition. Construction was broken down into two phases so deadlines connected with government stimulus funding could be met while funding for the remaining portion of the building’s budget was secured.
The south and east quadrangle wings formed the first phase and the west and north wings phase two. Construction on the first phase began in August 2009. The second phase began in 2011 and was initiated before the first one was complete. Phase one of the building was occupied while the second phase took place, says McLean.
The university often uses phased construction for major building renovations; this marked the first time they had used it for a new building. They combined it with a construction management approach that employs sequential tendering of the major sub-trades instead of the more conventional design/bid/build process.
The approach allowed them to start construction before the design was complete and accelerated the construction schedule to meet the tight deadlines.
“I think that’s probably the key,” says Armstrong.
“Because we had to meet mandated timelines both from the stimulus funding and obviously the school’s desire to be up and running.”
He estimates that it would have meant another year if they had adopted a more conventional approach to project management.
But construction management has its drawbacks. Although bids are compared to the cost estimates, they come in at different times, “so we never have a real handle on what the total construction costs will be,” McLean says. Costing is further complicated because not having a completed design means that some of the earlier bid packages have to “capture changes that come along later on in the design and construction process.”
EllisDon performed the combined role of construction manager and general contractor — another management modification. They were responsible for retaining all of the subcontractors through a competitive bidding process. That presented yet another challenge.
“There was no guarantee in phase two that we were going to get the same subcontractors that we did in phase one,” says McLean.
To address the problem, the company asked the phase one subcontractors to also provide pricing for phase two, he says.
The company’s combined role within the context of the phased construction process meant it could contribute its perspective while the project was still in development and assess the design’s “constructability,” Armstrong says, “and try to look for ways to perhaps simplify construction, make it more effective and hence more cost effective as well.”
Many others, ranging from building science consultants, cost consultants and the project’s LEED consultant also had a chance to contribute during the project’s formative stages.
“So all of this design and construction expertise was on the project before the design was completed,” says McLean.
The building is now substantially complete and was formally opened in September. McLean says remaining elements, such as the completion of landscaping, an exterior reflecting pool and the business library will be complete by the fall.
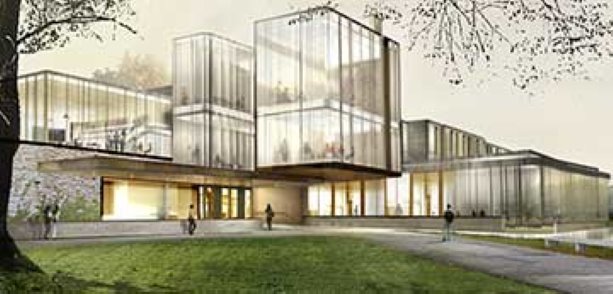
Recent Comments
comments for this post are closed